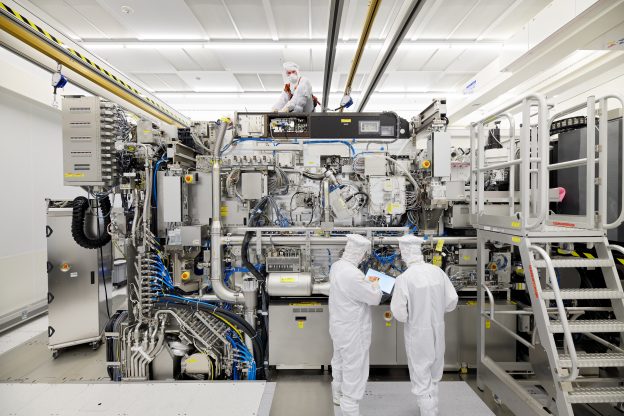
As TSMC, Samsung, and Intel compete fiercely in the race for 2nm advanced processes, a new wave of the “battle for crucial equipment” is simultaneously unfolding.
According to South Korean reports, ASML, the leader in semiconductor advanced lithography equipment, plans to manufacture ten equipment capable of producing 2nm chips next year, while aiming to increase its annual production capacity to 20 devices in the coming years.
Intel has secured up to six of the 10, taking the lead, while Samsung is also actively pursuing the procurement of the equipment. TSMC faces significant pressure in this competitive landscape.
South Korean tech media SamMobile has unveiled that as major semiconductor manufacturers announce plans to start producing 2nm chips in 2025, ASML is set to unveil equipment capable of manufacturing chips using the 2nm process in the coming months.
The latest extreme ultraviolet (EUV) lithography equipment is expected to increase the numerical aperture (NA) from 0.33 to 0.55. This enhancement improves the light-collecting capability of the optical system, enabling semiconductor fabs to utilize advanced patterning techniques for the production of 2nm process chips.
ASML is the sole global manufacturer of advanced EUV equipment for processes at 7nm. These equipment are not only expensive, costing several million dollars each, but they also have limited production capacity.
It has led to high demand from major semiconductor manufacturers like Samsung, Intel, and TSMC. Currently, only five chipmakers globally, including TSMC, Samsung, SK Hynix, Intel, and Micron, require EUV equipment, with TSMC accounting for 70% of EUV purchases.
Consequently, Samsung is actively pursuing collaboration and has signed a historic agreement with ASML to jointly invest KRW 1 trillion (approximately USD 755 million) in establishing a research and development facility in South Korea.
This collaboration aims to contribute to the development of Samsung’s 2nm process. Samsung plans to commence the production of 2nm process chips by the end of 2025 after acquiring the 2nm manufacturing equipment.
Samsung Electronics Vice Chairman Kyung Kye-hyun, who heads the Device Solutions Division, emphasized that the new agreement with ASML will assist Samsung in acquiring the next-generation high NA EUV equipment.
Kyung said, “Samsung has secured a priority over the High-NA equipment technology. (From the trip), I believe we created an opportunity for us to optimize the usage of High-NA technology for our production of DRAM memory chips and logic chips in the long term.”
On the Intel front, as part of its IDM 2.0 strategy, it is executing a 5 nodes in four years process development plan. Intel emphasizes that its Intel 20A process is progressing towards volume production readiness as planned, while the Intel 18A process is scheduled to test production phase in the first quarter of next year.
Facing the strong competition from Samsung and Intel, TSMC is not sitting idle. According to reports citing from Financial Times, TSMC has showcased its 2nm prototype test results to major clients like Apple and NVIDIA.
TSMC previously mentioned in its earnings call that it expects the 2nm process to enter mass production as scheduled in 2025. The company’s 2nm backside power rail solution is scheduled for the latter half of 2025, with mass production slated for 2026.
(Photo credit: ASML)
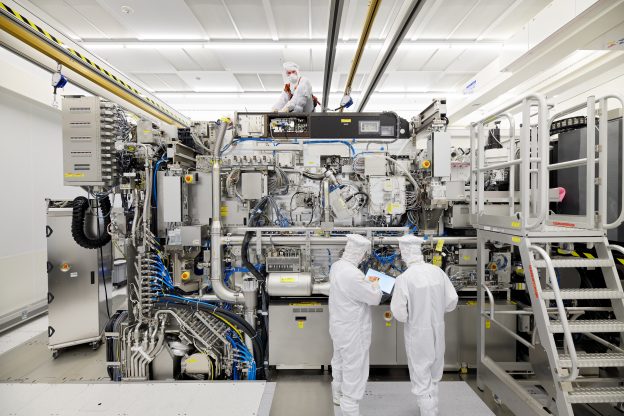
[News] The Battle on Advanced Processes Intensifies as ASML Plans to Produce Ten Equipment Capable of 2nm Chip Production Next Year | TrendForce Insights
As TSMC, Samsung, and Intel compete fiercely in the race for 2nm advanced processes, a new wave of the "battle for crucial equipment" is simultaneousl...
