U.S. forecast to increase its domestic chip manufacturing by 203% in the decade following enactment of the CHIPS and Science Act—and expand its share of the world’s total fab capacity for the first time in decades—according to new Semiconductor Industry Association/Boston Consulting Group report focused on the global chip supply chain
WASHINGTON—May 8, 2024—The Semiconductor Industry Association (SIA), in partnership with the Boston Consulting Group (BCG), today released a report on the global chip supply chain that projects the United States will triple its domestic semiconductor manufacturing capacity from 2022—when the CHIPS and Science Act (CHIPS) was enacted—to 2032. The projected 203% growth is the largest projected percent increase in the world over that time.
The study, titled “Emerging Resilience in the Semiconductor Supply Chain,” also projects the U.S. will grow its share of advanced logic (below 10nm) manufacturing to 28% of global capacity by 2032, up from 0% in 2022. Additionally, America is projected to capture over one-quarter (28%) of total global capital expenditures (capex) from 2024-2032, ranking second only to Taiwan (31%). In the absence of the CHIPS Act, the U.S. would have captured only 9% of global capex by 2032, according to the report.
While the report finds investments from the industry—facilitated by CHIPS incentives—are on track to reinvigorate semiconductor manufacturing in America and reinforce U.S. chip supply chains, it also identifies policy actions that will further strengthen supply chains, support R&D and chip design, grow the semiconductor workforce, and ensure CHIPS delivers maximum benefits to America’s economic and national security.
The report also analyzes the efforts underway in other countries to incentivize chip production and innovation and the criticality of ensuring chip companies have open access to global customers and suppliers, among other topics.
“Effective policies, such as the CHIPS and Science Act, are spurring more investments in the U.S. semiconductor industry. These investments will help America grow its share of global semiconductor production and innovation, furthering economic growth and technological competitiveness,” said Rich Templeton, Chairman of the Board at Texas Instruments and SIA board chair. “Continued and expanded government-industry collaboration will help ensure we build on this momentum and continue our next steps forward.”
Other key report findings:
Further, the study highlights the ways in which governments and companies are taking concerted action to increase resilience. The U.S. CHIPS Act committed $39 billion in incentives for semiconductor manufacturing, plus a separate advanced manufacturing investment tax credit. The European Union unveiled the European CHIPS Act, China initiated the third phase of its Integrated Circuit (IC) Industry Investment Fund, and various other incentive programs have emerged in Taiwan, Korea, Japan, India, and around the world. In parallel, companies have made significant investments, in both established and new regions. The report projects around $2.3 trillion in capex in 2024-2032, compared to $720 billion in the decade prior to enactment of the CHIPS Act (2013-2022).
Despite the progress made to strengthen U.S.-based semiconductor manufacturing, additional government policy actions are needed to help ensure America stays on track to address lingering supply chain vulnerabilities and grow its share of fabrication capacity, while also increasing its strength in areas such as advanced logic, design, EDA, and equipment in the face of growing global competition.
“The CHIPS and Science Act has put America on course to significantly strengthen domestic semiconductor production and R&D, but more work is needed to finish the job,” said John Neuffer, SIA president and CEO. “We look forward to working with government leaders to advance policies that broaden the STEM talent pipeline, invest in scientific research, promote free trade and access to global markets, and expand and extend critical CHIPS incentives.”
The CHIPS Act’s manufacturing incentives have sparked substantial announced investments in the U.S. In fact, companies in the semiconductor ecosystem have announced more than 80 new projects across 25 U.S. states—totaling nearly $450 billion in private investments—since the CHIPS Act was introduced. These announced projects will create more than 56,000 jobs in the semiconductor ecosystem and support hundreds of thousands of additional U.S. jobs throughout the U.S. economy.
www.semiconductors.org
WASHINGTON—May 8, 2024—The Semiconductor Industry Association (SIA), in partnership with the Boston Consulting Group (BCG), today released a report on the global chip supply chain that projects the United States will triple its domestic semiconductor manufacturing capacity from 2022—when the CHIPS and Science Act (CHIPS) was enacted—to 2032. The projected 203% growth is the largest projected percent increase in the world over that time.
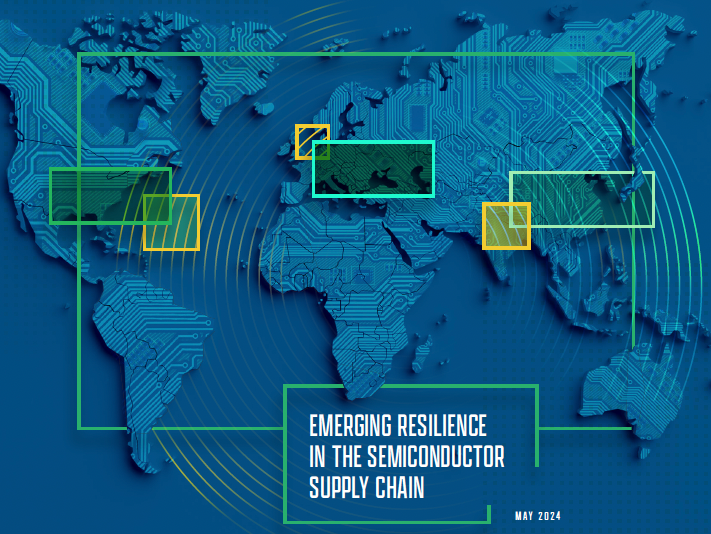
The study, titled “Emerging Resilience in the Semiconductor Supply Chain,” also projects the U.S. will grow its share of advanced logic (below 10nm) manufacturing to 28% of global capacity by 2032, up from 0% in 2022. Additionally, America is projected to capture over one-quarter (28%) of total global capital expenditures (capex) from 2024-2032, ranking second only to Taiwan (31%). In the absence of the CHIPS Act, the U.S. would have captured only 9% of global capex by 2032, according to the report.
While the report finds investments from the industry—facilitated by CHIPS incentives—are on track to reinvigorate semiconductor manufacturing in America and reinforce U.S. chip supply chains, it also identifies policy actions that will further strengthen supply chains, support R&D and chip design, grow the semiconductor workforce, and ensure CHIPS delivers maximum benefits to America’s economic and national security.
The report also analyzes the efforts underway in other countries to incentivize chip production and innovation and the criticality of ensuring chip companies have open access to global customers and suppliers, among other topics.
“Effective policies, such as the CHIPS and Science Act, are spurring more investments in the U.S. semiconductor industry. These investments will help America grow its share of global semiconductor production and innovation, furthering economic growth and technological competitiveness,” said Rich Templeton, Chairman of the Board at Texas Instruments and SIA board chair. “Continued and expanded government-industry collaboration will help ensure we build on this momentum and continue our next steps forward.”
Other key report findings:
- America’s world-leading 203% projected increase in fab capacity from 2022 to 2032 stands in stark contrast to its modest 11% increase from the previous decade (2012-2022), which ranked last among all major chip-producing regions, according to the SIA/BCG report.
- The U.S. share of the world’s chip manufacturing capacity will increase from 10% in 2022—when the CHIPS and Science Act was enacted—to 14% by 2032, marking the first time in decades the U.S. has grown its domestic chip manufacturing footprint relative to the rest of the world. In the absence of CHIPS enactment, the U.S. share would have slipped further to 8% by 2032, according to the report.
- The U.S. continues to lead the world in its overall contribution to the global value chain, with strong leadership positions in high value-added areas of semiconductor technology, including chip design, electronic design automation (EDA), and semiconductor manufacturing equipment.
Further, the study highlights the ways in which governments and companies are taking concerted action to increase resilience. The U.S. CHIPS Act committed $39 billion in incentives for semiconductor manufacturing, plus a separate advanced manufacturing investment tax credit. The European Union unveiled the European CHIPS Act, China initiated the third phase of its Integrated Circuit (IC) Industry Investment Fund, and various other incentive programs have emerged in Taiwan, Korea, Japan, India, and around the world. In parallel, companies have made significant investments, in both established and new regions. The report projects around $2.3 trillion in capex in 2024-2032, compared to $720 billion in the decade prior to enactment of the CHIPS Act (2013-2022).
Despite the progress made to strengthen U.S.-based semiconductor manufacturing, additional government policy actions are needed to help ensure America stays on track to address lingering supply chain vulnerabilities and grow its share of fabrication capacity, while also increasing its strength in areas such as advanced logic, design, EDA, and equipment in the face of growing global competition.
“The CHIPS and Science Act has put America on course to significantly strengthen domestic semiconductor production and R&D, but more work is needed to finish the job,” said John Neuffer, SIA president and CEO. “We look forward to working with government leaders to advance policies that broaden the STEM talent pipeline, invest in scientific research, promote free trade and access to global markets, and expand and extend critical CHIPS incentives.”
The CHIPS Act’s manufacturing incentives have sparked substantial announced investments in the U.S. In fact, companies in the semiconductor ecosystem have announced more than 80 new projects across 25 U.S. states—totaling nearly $450 billion in private investments—since the CHIPS Act was introduced. These announced projects will create more than 56,000 jobs in the semiconductor ecosystem and support hundreds of thousands of additional U.S. jobs throughout the U.S. economy.
America Projected to Triple Semiconductor Manufacturing Capacity by 2032, the Largest Rate of Growth in the World
U.S. forecast to increase its domestic chip manufacturing by 203% in the decade following enactment of the CHIPS and Science Act—and expand its share of the w
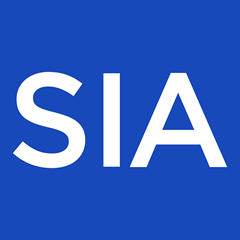