Taichung, TaiwanCNN —
Until just a few years ago, the world’s largest chipmaker had a simple answer to training new recruits — a buddy system that paired them up with senior engineers tasked with showing them the ropes.
All that changed three years ago, when a global chip shortage and rising geopolitical tension turbocharged growth at TSMC. It needed to create an intensive training program to get tens of thousands of new recruits to work quickly.
TSMC set up the Newcomer Training Center inside a sprawling science park in the city of Taichung in central Taiwan in 2021. That facility now holds the key to the company’s global expansion.
In a world dominated by Moore’s Law — the idea that the number of transistors on microchips would double every two years — speed is of the essence for TSMC and its customers, including Apple, Nvidia and AMD. It also matters for US President Joe Biden, who is counting on the company to boost US manufacturing in Arizona.
Today, all new engineers based in Taiwan and some overseas hires are required to spend eight weeks at the center, which CNN visited recently.
“[Now], we can teach the newcomers more systematically. We can make them learn faster and build a solid foundation,” said Marcus Chen, an instructor at the center. “It’s a TSMC core value [that] we have to do everything very efficiently.”
The center is modeled on the operations of a fabrication plant, called fabs, where chips are made.
In one room, a rotating robotic arm cleans and polishes a semiconductor wafer by pressing it on a pad, in a process known as chemical-mechanical polishing. In another, a machine lifts a pack of wafers to the ceiling and moves it around the facility.
“Every new fab, at the very beginning, we need to bring a certain percentage of people from Taiwan,” Lora Ho, the company’s senior vice president of human resources, told CNN. “After many years, what we want to do is to gradually reduce assignees [and] increase the local hires.”
The Newcomer Training Center opened in 2021.
Sometimes called the most important company in the world, TSMC (officially Taiwan Semiconductor Manufacturing Company) produces an estimated 90% of the world’s super-advanced semiconductor chips, which are used to power everything from smartphones to artificial intelligence applications.
To meet rising demand and facing pressure to be physically closer to its customers, TSMC is building new fabs in the United States, Japan and Germany. Its existing plants are in Taiwan as well as in eastern China and Washington state.
Last month, the chip giant opened its first fab in the Japanese city of Kumamoto and is set to open two $40 billion facilities in Phoenix, Arizona in the coming years to make smaller, more advanced chips. It has committed to investing $3.8 billion to build a fab in Dresden, Germany, the company’s first in Europe.
The soaring demand, particularly for chips that power AI, has created a shortage of talent for the semiconductor industry. TSMC said last year that one of its fabs in Arizona would be delayed because of a lack of specialist workers.
“Finding the best talent has always been an issue but it has become even more so since the world suddenly woke up in the past few years and realized semiconductors were important,” said Stewart Randall, head of electronics and embedded software at Intralink, a consultancy.
“Expanding fab numbers [and] capacity of fabs is connected to geopolitics but also market demand,” he added. “This means we need more people with IC (integrated circuits or semiconductor) design, IC manufacturing, materials science skills. Countries compete for this talent.”
TSMC’s Ho said a shortage of talent is one of the main challenges the company faces.
“There’s a scarcity of talent worldwide,” she said. “If we move globally, then we really need to expand our talent pool.”
TSMC currently has about 77,000 employees around the world. In a few years, the number will reach 100,000, Ho added.
While its engineers in Taiwan are paid extremely well, the job is demanding with long hours and weekend shifts. And, if an earthquake were to hit the island — a common occurrence — engineers are expected to return to their stations immediately, regardless of the time of day.
The Newcomer Training Center is built to resemble a fab.
Kristy Hsu, director of the Taiwan ASEAN Studies Center at the Chung-hua Institution for Economic Research, said that while Taiwanese employees may be accustomed to overtime and being on-call, other workers may not.
“For chip fabrication, and also testing and packaging, it’s a very labor-intensive industry, and therefore, people have … to work overtime,” she said. “Also, you have to always be prepared to be called [in], whether it’s during Chinese New Year or Christmas.”
“That working culture has been [in] Taiwan and some other East Asian countries like Japan for generations,” she added. “When you talk about this kind of work culture in the US and Germany, it’s going to be more problematic.”
Ho said as TSMC expands globally, it is learning how it should manage teams differently and efficiently from various parts of the world.
“We do need to adjust to the local practice and become socially acceptable. Certain things you can do here, but you cannot do there,” she said. “The way we manage in Taiwan cannot be totally transferred [to other countries]. In the US, we have to adjust to local culture.”
“People here [in Taiwan] are willing to follow the instruction. But I think in the US, you have to explain why — in the language that they’re familiar with,” she added.
The chip giant’s move to diversify its production beyond Taiwan has rattled the nerves of some locals, including lawmakers, who worry that it could eventually diminish the island’s importance as a global semiconductor powerhouse.
Ho played down those concerns.
“I don’t think it will take away [Taiwan’s] strengths because we are still very highly concentrated in Taiwan, and the most leading-edge technology will absolutely start from Taiwan,” she said. “It’s not taking away, but it will expand Taiwan’s exposure and we can learn how to operate globally.”
— CNN’s Juliana Liu contributed reporting.
Until just a few years ago, the world’s largest chipmaker had a simple answer to training new recruits — a buddy system that paired them up with senior engineers tasked with showing them the ropes.
All that changed three years ago, when a global chip shortage and rising geopolitical tension turbocharged growth at TSMC. It needed to create an intensive training program to get tens of thousands of new recruits to work quickly.
TSMC set up the Newcomer Training Center inside a sprawling science park in the city of Taichung in central Taiwan in 2021. That facility now holds the key to the company’s global expansion.
In a world dominated by Moore’s Law — the idea that the number of transistors on microchips would double every two years — speed is of the essence for TSMC and its customers, including Apple, Nvidia and AMD. It also matters for US President Joe Biden, who is counting on the company to boost US manufacturing in Arizona.
Today, all new engineers based in Taiwan and some overseas hires are required to spend eight weeks at the center, which CNN visited recently.
“[Now], we can teach the newcomers more systematically. We can make them learn faster and build a solid foundation,” said Marcus Chen, an instructor at the center. “It’s a TSMC core value [that] we have to do everything very efficiently.”
The center is modeled on the operations of a fabrication plant, called fabs, where chips are made.
In one room, a rotating robotic arm cleans and polishes a semiconductor wafer by pressing it on a pad, in a process known as chemical-mechanical polishing. In another, a machine lifts a pack of wafers to the ceiling and moves it around the facility.
A growing problem
The engineers trained at the center won’t just be deployed across TSMC’s fabs in Taiwan. Some will be used to “seed” its facilities globally.“Every new fab, at the very beginning, we need to bring a certain percentage of people from Taiwan,” Lora Ho, the company’s senior vice president of human resources, told CNN. “After many years, what we want to do is to gradually reduce assignees [and] increase the local hires.”
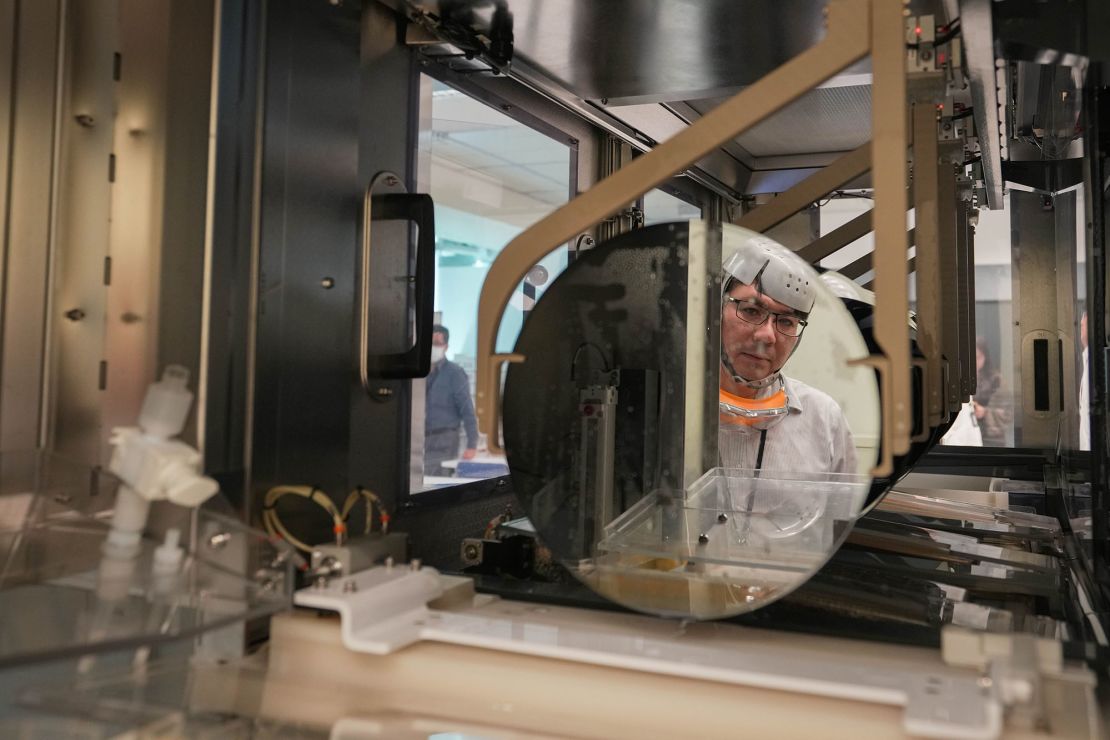
The Newcomer Training Center opened in 2021.
Sometimes called the most important company in the world, TSMC (officially Taiwan Semiconductor Manufacturing Company) produces an estimated 90% of the world’s super-advanced semiconductor chips, which are used to power everything from smartphones to artificial intelligence applications.
To meet rising demand and facing pressure to be physically closer to its customers, TSMC is building new fabs in the United States, Japan and Germany. Its existing plants are in Taiwan as well as in eastern China and Washington state.
Last month, the chip giant opened its first fab in the Japanese city of Kumamoto and is set to open two $40 billion facilities in Phoenix, Arizona in the coming years to make smaller, more advanced chips. It has committed to investing $3.8 billion to build a fab in Dresden, Germany, the company’s first in Europe.
The soaring demand, particularly for chips that power AI, has created a shortage of talent for the semiconductor industry. TSMC said last year that one of its fabs in Arizona would be delayed because of a lack of specialist workers.
“Finding the best talent has always been an issue but it has become even more so since the world suddenly woke up in the past few years and realized semiconductors were important,” said Stewart Randall, head of electronics and embedded software at Intralink, a consultancy.
“Expanding fab numbers [and] capacity of fabs is connected to geopolitics but also market demand,” he added. “This means we need more people with IC (integrated circuits or semiconductor) design, IC manufacturing, materials science skills. Countries compete for this talent.”
TSMC’s Ho said a shortage of talent is one of the main challenges the company faces.
“There’s a scarcity of talent worldwide,” she said. “If we move globally, then we really need to expand our talent pool.”
TSMC currently has about 77,000 employees around the world. In a few years, the number will reach 100,000, Ho added.
Culture shock
A lack of qualified workers isn’t the only problem. TSMC has also faced challenges in adapting to differences in work culture between Asian and Western countries.While its engineers in Taiwan are paid extremely well, the job is demanding with long hours and weekend shifts. And, if an earthquake were to hit the island — a common occurrence — engineers are expected to return to their stations immediately, regardless of the time of day.
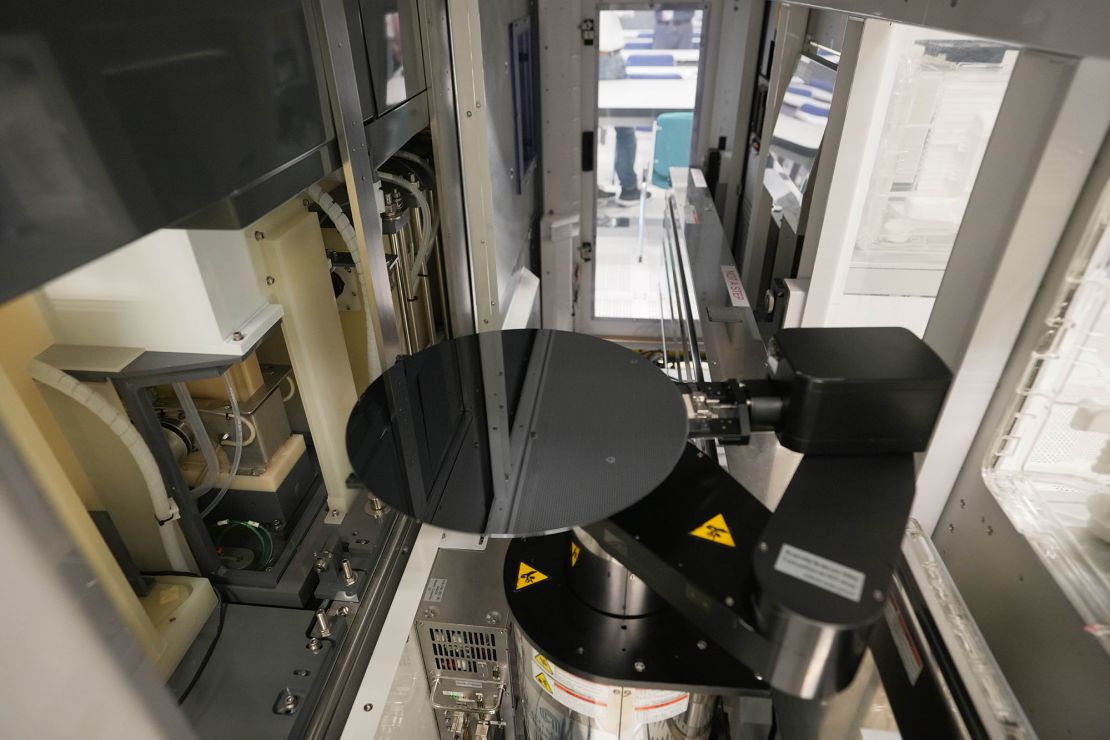
The Newcomer Training Center is built to resemble a fab.
Kristy Hsu, director of the Taiwan ASEAN Studies Center at the Chung-hua Institution for Economic Research, said that while Taiwanese employees may be accustomed to overtime and being on-call, other workers may not.
“For chip fabrication, and also testing and packaging, it’s a very labor-intensive industry, and therefore, people have … to work overtime,” she said. “Also, you have to always be prepared to be called [in], whether it’s during Chinese New Year or Christmas.”
“That working culture has been [in] Taiwan and some other East Asian countries like Japan for generations,” she added. “When you talk about this kind of work culture in the US and Germany, it’s going to be more problematic.”
Ho said as TSMC expands globally, it is learning how it should manage teams differently and efficiently from various parts of the world.
“We do need to adjust to the local practice and become socially acceptable. Certain things you can do here, but you cannot do there,” she said. “The way we manage in Taiwan cannot be totally transferred [to other countries]. In the US, we have to adjust to local culture.”
“People here [in Taiwan] are willing to follow the instruction. But I think in the US, you have to explain why — in the language that they’re familiar with,” she added.
The chip giant’s move to diversify its production beyond Taiwan has rattled the nerves of some locals, including lawmakers, who worry that it could eventually diminish the island’s importance as a global semiconductor powerhouse.
Ho played down those concerns.
“I don’t think it will take away [Taiwan’s] strengths because we are still very highly concentrated in Taiwan, and the most leading-edge technology will absolutely start from Taiwan,” she said. “It’s not taking away, but it will expand Taiwan’s exposure and we can learn how to operate globally.”
— CNN’s Juliana Liu contributed reporting.