My first IR drop analysis was back in the early 1980s at Intel, where I had to manually model the parasitics of the VDD and VSS interconnect for all of the IO cells that our team was designing in a graphics chip, then I ran that netlist in a SPICE simulator using transient analysis, measuring the bounce in VSS and droop in VDD levels as all of the IOs switched simultaneously to keep the power and ground levels within a safe operating region. On another occasion in 1980 I was debugging a DRAM chip, because a certain percentage of these chips were failing when a specific portion of the aluminum wiring heated up enough to cause the metal to bubble and form open circuits, an Electromigration (EM) failure. Oh, how I wished for some EDA tools to help me pinpoint reliability issues like EM/IR, before tape-out of course.
For the past few decades there have been EM/IR tools available in the EDA market, mostly for big digital designs and limited analog designs, so reliability analysis has been performed in order to avoid field failures. Last week I had a Microsoft Teams meeting with Joseph Davis of Siemens EDA, where he outlined their brand new EM/IR tool offering, called mPower.
The past approaches to EM/IR analysis have been to use static techniques on big analog blocks, which is faster, but less accurate than dynamic analysis. Then for smaller blocks, typically analog or AMS, to use the more accurate dynamic analysis. What jumped out to me right away with the new mPower tool, is that it has the capacity to handle the full-chip using the more accurate dynamic analysis, as shown below:
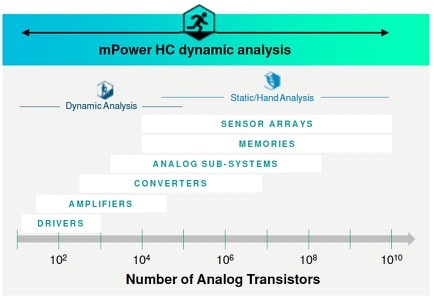
The secret sauce to mPower is in how it scales across your network of CPUs, creating quick run times and enabling billion transistor capacity, while also minimizing RAM usage. Inputs to mPower are industry standard file formats, so there’s little work for your CAD group, and it’s a quick learning curve for your design engineers using the tool, just pick out your favorite extraction tool and SPICE circuit simulator. Siemens EDA does offer the popular Calibre tool for extraction and AFS for SPICE circuit simulation, but really, any vendor tool works.
For digital flows, there’s the mPower Digital tool, and then for transistor-level analog flows, the product is mPower Analog. I asked about which IC design companies are using mPower for EM/IR analysis, and was impressed with the initial list:
- MaxLinear – full-chip, large analog
- Efinix FPGA – full-chip, transistor-level EM/IR analysis without IP modeling
- Esperanto – AI chip with 1,000+ RISC-V cores, ran mPower Digital on their own network
- On Semi – pixel array designs, both mPower Digital and Analog
The AI chip from Esperanto has 24 billion transistors, so that’s a prime example showing the capacity of the mPower Digital tool. The other customer examples just couldn’t be run with competitor tools using the dynamic approach.
Support from foundries will be announced soon, just know that you can use this new EM/IR tool at process nodes down to 5nm with confidence today, and that 3nm support is in the works. Even 2.5 or 3D ICs can be analyzed for EM/IR compliance, and you can run mPower Digital in the cloud to meet your time to market requirements.
Summary
During IC layout and certainly before tape-out, your design team needs assurance that EM/IR reliability concerns have been analyzed, and that the layout has been properly updated. There is now a new choice for this type of analysis, and Siemens EDA has carved out some unique properties in this segment like full-chip dynamic analysis, using mPower Analog. It’s worth a look to see how your designs could benefit from higher capacity, and fit within the compute resources in place. EDA competition always fosters innovation, and vendor loyalties can quickly change, if the new entrant delivers on their promises.
Related Blogs
- A Custom Layout Environment for SOC Design Closure
- RealTime Digital DRC Can Save Time Close to Tapeout
- Transistor-Level Static Checking for Better Performance and Reliability
- Library Characterization: A Siemens Cloud Solution using AWS
Comments
There are no comments yet.
You must register or log in to view/post comments.