Power devices have historically been made from silicon (Si), which has reached the limit of electric power loss reduction. With the superior physical and electrical properties of silicon carbide (SiC), we can expect to see a significant expansion in the amount of electric power conversion of electrical equipment as well as reduced… Read More
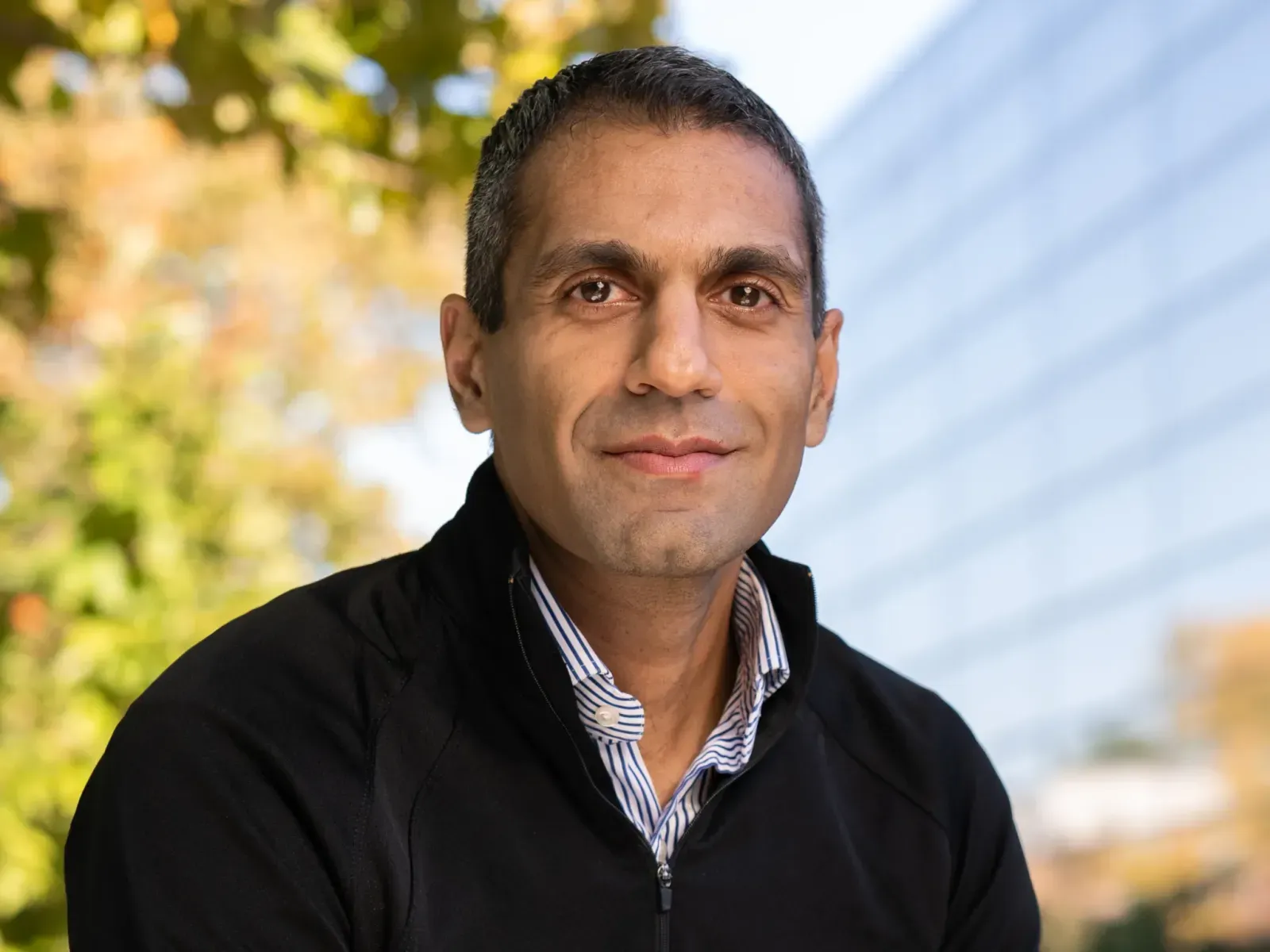
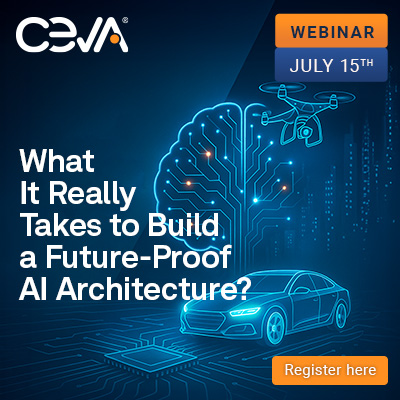
Intel’s 35% Density Advantage Claim Explored
The previous blog I did on the density difference between Intel 14nm and TSMC 20nm caused quite a stir and many interesting comments which I would like to address. After writing thousands of blogs on a wide variety of topics I have found that playing the devil’s advocate stimulates the most productive conversations and in this case… Read More
Who will be “lucky dog” in 4G LTE basebands?
The official term is “beneficiary rule”, but among colorful racing broadcasters, drivers, and fans it is more commonly referred to as the “lucky dog”: the driver who is down a lap, but gets to advance to the lead lap by virtue of being farthest ahead when a caution flag is raised.
Qualcomm has lapped the entire field when it comes to … Read More
MEMS+, Bringing MEMS into the Electronic World
One of the things about MEMS devices is that they almost always live on a chip that also contains the electronics necessary to process the output from the sensor. For example, an on-chip accelerometer for a car airbag deployment will contain the electronics necessary to process the signal from the sensor and end up with something… Read More
The SUN will NOT set on Oracle!
Larry Ellison resigning as CEO of Oracle caught me by surprise. I definitely did not see that one coming. Talk about the end of an era, as a 30+ year Silicon Valley veteran there have been quite a few industry icons that stand out amongst the others: Dave Packard, Bill Hewlett, Gordon Moore, Andy Grove, Bill Gates, Steve Jobs, and Larry… Read More
MIPI Alliance introduces C-PHY, Synopsys launch C-PHY VIP
The set of MIPI PHY specifications has enlarged during last night, as theMIPI Alliance has introduced the new C-PHY spec on September 17th, a physical layer interface for camera and display applications. “The MIPI C-PHY specification was developed to reduce the interface signaling rate to enable a wide range of high-performance… Read More
Ultra low light CMOS biosensor helps tackle infectious diseases
The recent outbreak of Ebola in West Africa underscores the urgent need for globally affordable tools to help fight infectious diseases. Among these, a method to rapidly and accurately identify the infectious pathogen is of particular importance.
In recent years, researchers have tried many ways to achieve easily portable … Read More
GlobalFoundries on the Road
Every year in the fall GlobalFoundries has a series of technical seminars they take on the road around the US. This year it kicks off on Tuesday, October 21 at the Doubletree Hotel in San Jose. Two days later it is at Dana Point (southern CA) and on the 30th it goes to Austin (you don’t need me to tell you where Austin is, I’m… Read More
Designing the Right Architecture Using HLS
With the advent of HLS tools, general notion which comes to mind is that okay, there’s an automated tool which can optimize your design description written in C++/SystemC and provide you a perfect RTL. In real life, it’s not so, any design description needs hardware designer’s expertise to adopt right algorithm and architecture… Read More
GLOBALFOUNDRIES Acquires IBM Semiconductor Unit!
I have it on pretty good authority that IBM has in fact come to terms with GLOBALFOUNDRIES on the sale of their semiconductor business. For those of you who have been following the story, especially the IBM semiconductor people, it has been a real roller coaster ride. If in fact this handshake deal goes through (expect a public announcement… Read More
TSMC N3 Process Technology Wiki