Let’s face it, designs are getting harder, much harder. Gone are the days when the electrical and mechanical design of a system occurred separately. Maybe ten years ago this practice was acceptable. Once the electrical design was completed (either the chip or the board) the parameters associated with the design were then given to the package or PCB design team to implement the physical delivery of the design. The handoff was done once, and each team lived in its own world. Those days are gone. In current day design complexity, the electrical design impacts the mechanical design in subtle ways. Similarly, the mechanical design of the system, including things like choice of materials has a profound impact on what is possible electrically. One must break down the walls and collaborate continuously, or accept the likelihood of project overruns and failure. A comprehensive and informative white paper was recently published on this topic for PCB design. Read on to understand achieving a unified electrical/mechanical PCB design flow – The Siemens Digital Industries Software view.
Why Now?
Entitled Unifying ECAD-MCAD PCB design through collaborative best practices, the Siemens white paper begins by setting the stage for why a unified PCB design flow is so important now. Most SemiWiki readers will be familiar with this trend. The overall demands for PCB design have also been discussed in detail in this SemiWiki post. The new Siemens white paper cites four trends in electronic design that are making a unified flow so urgent:
Compute power: Since the advent of the microprocessor, there’s been an astronomical increase in the compute power that chips can deliver – a trillion-fold over six decades. Given the slowing of Moore’s Law, future performance gains in semiconductors will be driven by, among other factors, advanced packaging flows.
Engineering discipline convergence: The “smaller, denser, faster” mantra associated with today’s products is magnifying the importance of ensuring that electromechanical compatibility is addressed prior to the first fabrication – waiting until manufacture to validate electronic and mechanical compatibility is clearly leaving things until too late.
Sustainability: The environmental impact of the manufacture of electronic devices is starting to get more scrutiny, as is the worldwide energy consumption of devices during their working life. This one is quite important to Siemens.
AI in electronics design: The fourth trend is the rise of AI in electronics design. AI might be considered a product of electronics, yet AI can also help with electronics design.
The white paper goes into a lot more detail on these topics. Links are coming so you can see the whole picture, as well as learn more about the Siemens approach.
What’s Needed?
The white paper covers a lot of ground. Here are some of the topics that are examined:
The importance of ECAD-MCAD collaboration: An integrated ECAD/MCAD collaboration environment enables electrical and mechanical design teams to work together throughout the entire design process in real time. And this can spell the margin of victory for a complex design project. The specific benefits of a well-integrated approach are discussed.
Ways ECAD-MCAD collaboration can be improved: A lot of engineering development teams still struggle to break free of legacy practices, which were perfectly good in their day but fall short in the present day. Specific approaches to improving the process are discussed.
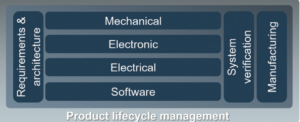
Keys to successful ECAD-MCAD collaboration: Efficient collaboration between ECAD and MCAD domains enables both to optimize an electronics design within tight form-factor constraints while still meeting quality, reliability, and performance requirements. In this section, specific approaches to design methodology and data sharing are presented. The goal is a multi-discipline, multi-domain workflow that supports real-time collaboration, as illustrated in the figure.
A toolkit for collaborative engineering: Now that some of the reasons collaboration is so important and some of the obstacles to its adoption have been discussed, this section looks at the solutions available to support ECAD- MCAD collaboration.
Accelerating PCB design: The Siemens Xcelerator business platform ecosystem is presented, with details of scope, capabilities, and benefits for design teams worldwide.
To Learn More
If you’re involved in complex system design this white paper is a must read. You can access the full text here. There is also a great podcast from the authors of the white paper available here. You can now learn about achieving a unified electrical/mechanical PCB design flow – The Siemens Digital Industries Software view.
Share this post via:
Comments
There are no comments yet.
You must register or log in to view/post comments.