“The amateurs discuss tactics: the professionals discuss logistics.”
— Napoleon
Logistics is even more important today than it was in the early 1800’s. Further, the effectiveness of Defense systems is increasingly driven by sophisticated electronics. As the recent Ukraine conflict reveals, weapons such as precision munitions, autonomous drones, and other similar systems generate asymmetrical advantages on the battlefield. However, all these systems also generate a massive and complex electronics logistical tail which must be managed carefully. For the electronics supply ecosystem, Defense falls into the broader category of Long Lifecycle (LLC) system products.
“Two Speed” Challenge
LLC (Long lifecycle) are products which need to be supported for many years – typically anything over five years or more. In this time, these products need to provide legacy part support, and rarely drive very high chip volumes. However, the economics of semiconductor design imply that custom semiconductors only make sense for markets with high volume. Today, this consists largely of the consumer (cell phone, laptop, tablet, cloud, etc) marketplace which are short lifecycle products with typical lifecycle of < 5 years. This hard economic fact has optimized the semiconductor industry towards consumer driven short lifecycle products. This is at odds with the requirement of long lifecycle products, both from frequent End-of-Life obsolescence and long-term product reliability. The reliability is further impacted in Defense by the fact that these components must perform under strenuous external environments with challenging thermal, vibration and even radiation conditions. This “Two Speed” challenge and results in very frequent failure and obsolescence of electronic components.
Move towards “Availability” Contracts in Aerospace & Défense
Traditionally in the aerospace and defense industry, an initial contract for development and manufacture is followed by a separate contract for spares and repairs. In the past, there has been a trend towards “availability” contracts where industry delivers a complete Product Service System (PSS). The key challenge in such contracts is to estimate “Whole Life Cost” (WLC) of the product which may span 30 or even 40 years. As one might imagine, this PSS paradigm skyrockets the cost of systems and still is not fool proof because of its need to predict the future. This has led to some embarrassing costs for defense part procurement as compared to the commercial equivalent.
The US Secretary of Defense William Perry memorandum in 1994 resulted in a move towards performance-based specifications which led to the virtual abandonment of the MIL-STD and MIL-SPEC system that had been the mainstay of all military procurement in the US for several decades. Coupled with “Diminishing Manufacturing Sources” (DMS) for military grade components, the imperative was to move towards COTS (Commercial Of the Shelf) components while innovating at system level to cater to the stringent operating environment requirements. The initial reasoning and belief in using COTS to circumvent system costs was effective. However, it did expose defense systems to some key issues.
Key Issues for Defense Industry today
- Component Obsolescence
Primarily as a result of “Two-Speed” challenge described above, components become harder to source over time and even grow obsolete and the rate of discontinuance of part availability is increasing steadily. Many programs such as the F22 stealth fighter, AWACS, Tornado, and Eurofighter are suffering from such component obsolescence. As a result, the OEM’s are forced to design replacements for those obsolete components and face nonrecurring engineering costs as a result. As per McKinsey’s recent estimates [“How industrial and aerospace and defense OEMs can win the obsolescence challenge, April 2022, McKinsey Insights” ], the aggregate obsolescence related nonrecurring costs for military aircraft segment alone are in the range of US $50 billion to US $70 billion.
- Whole Life Cost (WLC)
As mentioned above, with increasing move towards “availability” contracts in defense and aerospace, one of the huge challenges has been to compute a realistic “Whole Life Cost” (WLC) of the products through the product lifecycle. This leads to massive held inventory costs with associated waste when held inventory is no longer useful. Moreover, any good estimate of WLC will require an accurate prediction of the future.
- Reliability
Semiconductors for the consumer market are optimized for consumer lifetimes – typically 5 years or so. For LLC markets like Defense, the longer product life in non-traditional environmental situations often leads to product reliability and maintenance issues especially with increased use of COTS components.
- Logistics chain in forward deployed areas
One of the unique issues in Defense which is further accentuated due to increased move towards “availability” contracts is the logistics nightmare to support equipment deployed in remote forward areas. A very desirable characteristic would be to have “in theatre” maintenance and update capability for electronic systems. The last mile is the hardest mile in logistics.
- Future Function
Given the timeframes of interest, upgrades in functionality are virtually guaranteed to happen. Since Defense products often have the characteristic of being embedded in the environment, upgrade costs are typically very high. A classic example is one of a satellite where the upgrade cost is prohibitively high. Similarly with weapon systems deployed in forward areas, upgrade costs are prohibitive. Another example is obsolescence of industry standards and protocols and need to adhere to newer ones. In fact, field embedded electronics (more so in defense) require flexibility to manage derivative design function WITHOUT hardware updates. How does one design for this capability, and how does a program manager understand the band of flexibility in defining new products, derivatives, and upgrades?
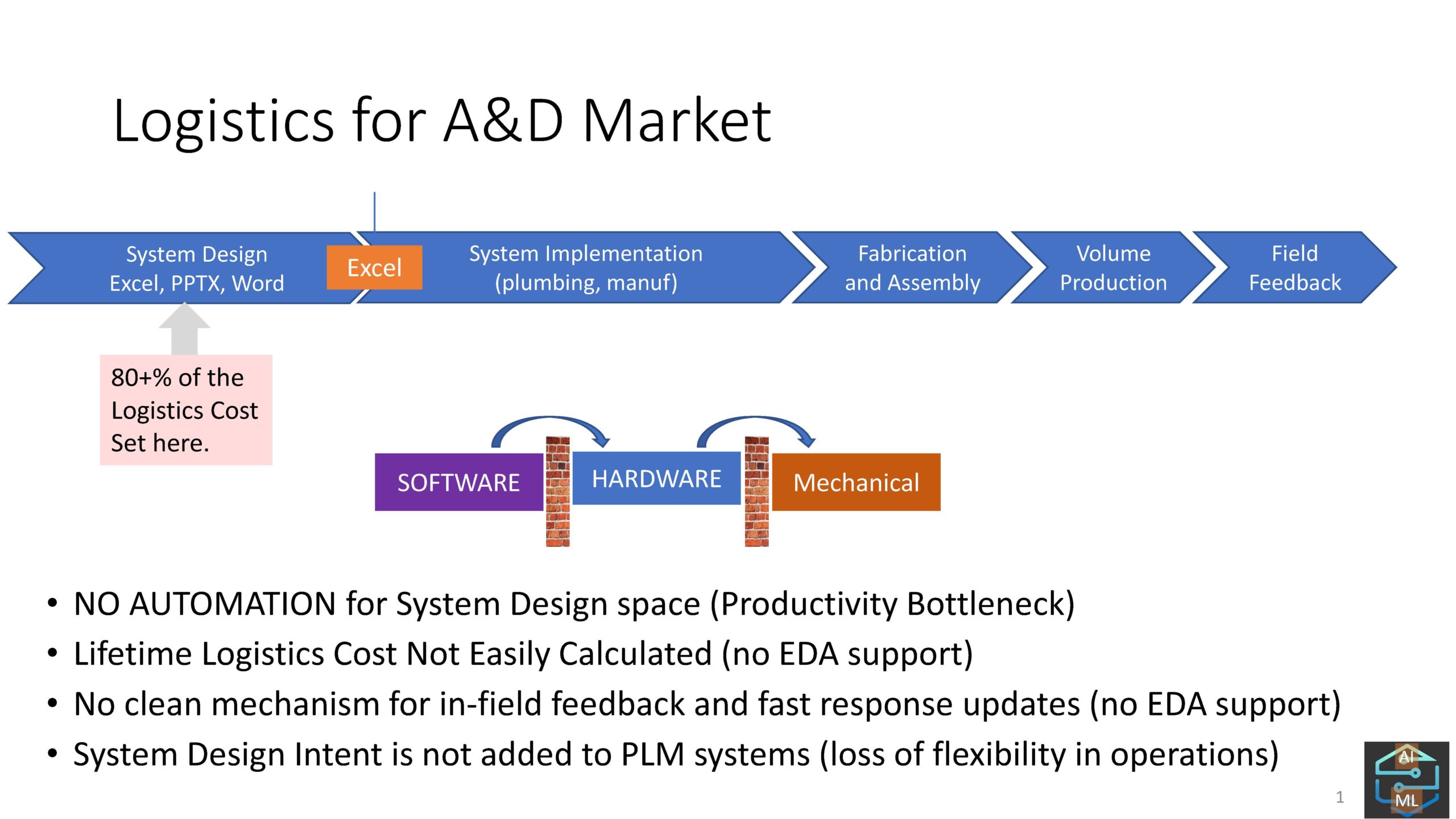
What is the solution to these issues? That answer there is the need to build a Design for Supply Chain methodology and associated Electronic Design Automation (EDA) capability.
Just as manufacturing test was optimized by “Designing for Test” and power optimized by “Designing for Power” or performance with “Design for performance” etc, one should be designing for “Supply Chain and Reliability”! What are the critical aspects of Design for Supply Chain capability?
- Programmable Semiconductor Parts: Programmable parts (CPU, GPU, FPGA, etc) have the distinct advantages of:
- Parts Obsolescence: A smaller number of programmable parts minimize inventory skews, can be forward deployed, and can be repurposed around a large number of defense electronic systems. Further, the aggregation of function around a small number of programmable parts raises the volume of these parts and thus minimizes the chances for parts obsolescence.
- Redundancy for Reliability: Reliability can be greatly enhanced by the use of redundancy within and of multiple programmable devices. Similar to RAID storage, one can leave large parts of an FPGA unprogrammed and dynamically move functionality based on detected failures.
- Future Function: Programmability enables the use of “over the air” updates which update functionality dynamically.
- Electronic Design Automation (EDA): To facilitate a design for supply chain approach, a critical piece is the EDA support. Critical functionality required is:
- Total Cost of Ownership Model: With LLCs, it is very important to consider lifetime costs based on downstream maintenance and function updates. An EDA system should help calculate lifetime cost metrics based on these factors to avoid mistakes which simply optimize near-term costs. This model has to be sophisticated enough to understand that derivative programmable devices often can provide performance/power increases which are favorable as compared to older technology custom devices.
- Programming Abstractions: Programmable devices are based on abstractions (computer ISA, Verilog, Analog models, etc) from which function is mapped onto physical devices. EDA functionality is critical to maintain these abstractions and automate the process of mapping which optimizes for power, performance, reliability, and other factors. Can these abstractions & optimizations further be extended to obsolescence?
- Static and Dynamic Fabrics: When the hardware configuration does not have to be changed, EDA functionality is only required for the programming the electronic system. However, if hardware devices require changes, there is a need for a flexible fabric to accept the updates in a graceful manner. The nature of the flexible fabric maybe mechanical (ex..rack-mountable boards) or chemical (quick respins of PCB which maybe done in-field). All of these methods have to be managed by a sophisticated EDA system. These methods are the key to the ease of integration of weapons systems.
With the above capability, one can perform proactive logistics management. One of the best practices that can yield rich dividends is to constitute a cross functional team (with representation from procurement, R&D, manufacturing and quality functions) which continuously scans for potential issues. This team can be tasked with developing set of lead indicators to assess components, identify near-term issues, and develop countermeasures. In order for this cross-functional programs to work, the EDA functionality has to be tied into the Product Lifecycle Management (PLM) systems in the enterprise.
Currently, a great deal of system intent is lost across the enterprise or over time as the design team moves to other projects. Thus, even the OEMs who use such proactive obsolescence management best practices are significantly hampered by lack of structured information or sophisticated tools which allow them to accurately predict these issues and plan mitigating actions including last-time strategic buys, finding alternate suppliers and even finding optimal FFF (Fit-Form-Function) replacements. It is imperative that such software (EDA) tool functions are available yesterday.
Summary
The semiconductor skew towards short lifecycle products (aka consumer electronics) has created a huge opportunity for the Defense industry to access low-cost electronics. However, this also generates issues when there is a need to support products in excess of 30 years as a result of fast obsolescence and shorter component reliability. What further worsens the situation for Defense are couple of unique situations for them – first, logistics issues in supporting equipment deployed on forward deployed areas and second, the increasing use of “availability” or full Product Service System contracts where establishing WLC (Whole Life Costs) for the equipment becomes critical. The only way this can be solved efficiently is to bring in a paradigm shift to “Design for Supply Chain” EDA innovation is needed to significantly enhance to support these levels of abstractions at system/PCB level and be a catalyst to bring in this paradigm shift. McKinsey estimated a 35% cost reduction in obsolescence related nonrecurring costs by only using a structured albeit still reactive obsolescence management methodology, a proactive “Design for Supply Chain” approach can be truly transformational.
Acknowledgements:
- Anurag Seth : Special thanks to Anurag for co-authoring this article.
- D. “Jake” Polumbo (Major General USAF (ret.)): Thanks for Review (https://www.twoblueaces.com/)
- Mark Montgomery (Executive Director): Thanks for Review (CyberSolarium.org)
Also Read:
INNOVA PDM, a New Era for Planning and Tracking Chip Design Resources is Born
Share this post via:
Flynn Was Right: How a 2003 Warning Foretold Today’s Architectural Pivot