Key Takeaways
- The increasing complexity of semiconductor chip design has made managing post-tapeout flow (PTOF) jobs a compute-intensive task, prompting foundries to seek scalable cloud solutions.
- Cloud platforms provide dynamic scaling, allowing foundries to pay only for resources used, thereby facilitating flexible management of PTOF workloads without substantial upfront investments.
- Strategic partnerships like the one between Siemens EDA and AWS enable semiconductor companies to optimize PTOF processes through automation, real-time cost control, and advanced features like GPU acceleration.
As semiconductor chips shrink and design complexity skyrockets, managing post-tapeout flow (PTOF) jobs has become one of the most compute-intensive tasks in manufacturing. Advanced computational lithography demands an enormous amount of computing power, putting traditional in-house resources to the test. Enter the cloud—an agile, scalable solution with hundreds of compute options, set to revolutionize how foundries manage PTOF workloads.
The unpredictability problem: Bridging the gap in resources
For years, foundries have relied on powerful in-house resources to handle PTOF tasks. But PTOF workloads aren’t consistent—sometimes demand surges, leading to waiting queues that delay production, while at other times, costly resources sit idle. Expanding on-premises infrastructure to match peak demand is both costly and slow, often taking months to deploy. In an industry where every day counts, finding a flexible solution is essential. This is where the cloud steps in, offering dynamic scaling and the freedom to match resources with demand as needed.
Cloud elasticity: Pay only for what you need
This on-demand scaling means foundries no longer must overprovision or commit to massive hardware investments upfront. Cloud platforms are transforming PTOF workflows by allowing foundries to pay only for what they use. With infrastructure managed by cloud providers, teams can shift their focus to developing applications and improving customer engagement while resources expand, or contract as needed. Cloud services offer semiconductor companies access to a global network of tools, empowering them to adapt quickly and push the boundaries of innovation.
Scaling up seamlessly: Siemens EDA and AWS join forces
This vision of agility and scalability became a reality in July 2023, when Siemens EDA and AWS signed a Strategic Collaboration Agreement to accelerate EDA workloads in the cloud. Out of this partnership came Cloud Flight Plans—automation scripts and best practices that streamline EDA deployment on AWS. Now, semiconductor manufacturers can effortlessly scale up resources, deploying hundreds of thousands of cores on demand. No more waiting months to expand data centers; cloud resources are available instantly, without capital investments or maintenance.
Building the foundation: A reference architecture for PTOF in the cloud
This agility is enhanced by Siemens EDA’s Cloud Reference Environment, an architecture purpose-built to handle PTOF jobs on AWS. Designed with secure principles and optimized for seamless workload management, this setup dynamically scales resources based on current demand. A central management system allocates resources to high-priority jobs and quickly redirects any underutilized capacity. Real-time spending insights empower semiconductor companies to control their cloud costs, ensuring resources are optimized at every step and that budget surprises are a thing of the past.
Real-time cost control with CalCM+: Smart scaling for smarter budgets
But it’s not just about scaling—it’s also about managing those costs smartly. Enter CalCM+, a
solution for maximizing cloud efficiency of Calibre PTOF jobs. Central to CalCM+ is adaptive resource management, which monitors active jobs and allocates resources based on actual demand. This intelligent scaling ensures resources aren’t wasted on overprovisioning, keeping budgets lean.
At the heart of CalCM+ is the cost calculation app, offering real-time spending insights by integrating directly with AWS pricing and the Slurm scheduler. Teams can track job costs in real-time, make informed decisions, and optimize resources based on precise needs. A recent study (see chart below) highlights how CalCM+ delivers measurable cost savings through smart scaling and predictive insights, proving that cloud efficiency is as much about cost control as it is about performance.
Data-driven insights: Predicting the future of resource use
CalCM+ goes a step further with a data analysis module that records usage metrics and job metadata, enabling predictions for future jobs. By studying historical data, this tool provides insights into expected runtime and memory usage, allowing teams to pick the best instance types for each task.
Lean Computing
The AUTOREVOKECYCLE feature dynamically releases underutilized CPUs and reallocates them to high-demand jobs. This lean computing approach doesn’t just keep costs down—it ensures resources are used precisely where they’re needed, avoiding the waste that comes from overprovisioning. Figure 1 shows the effect of using the AUTOREVOKECYCLE feature.
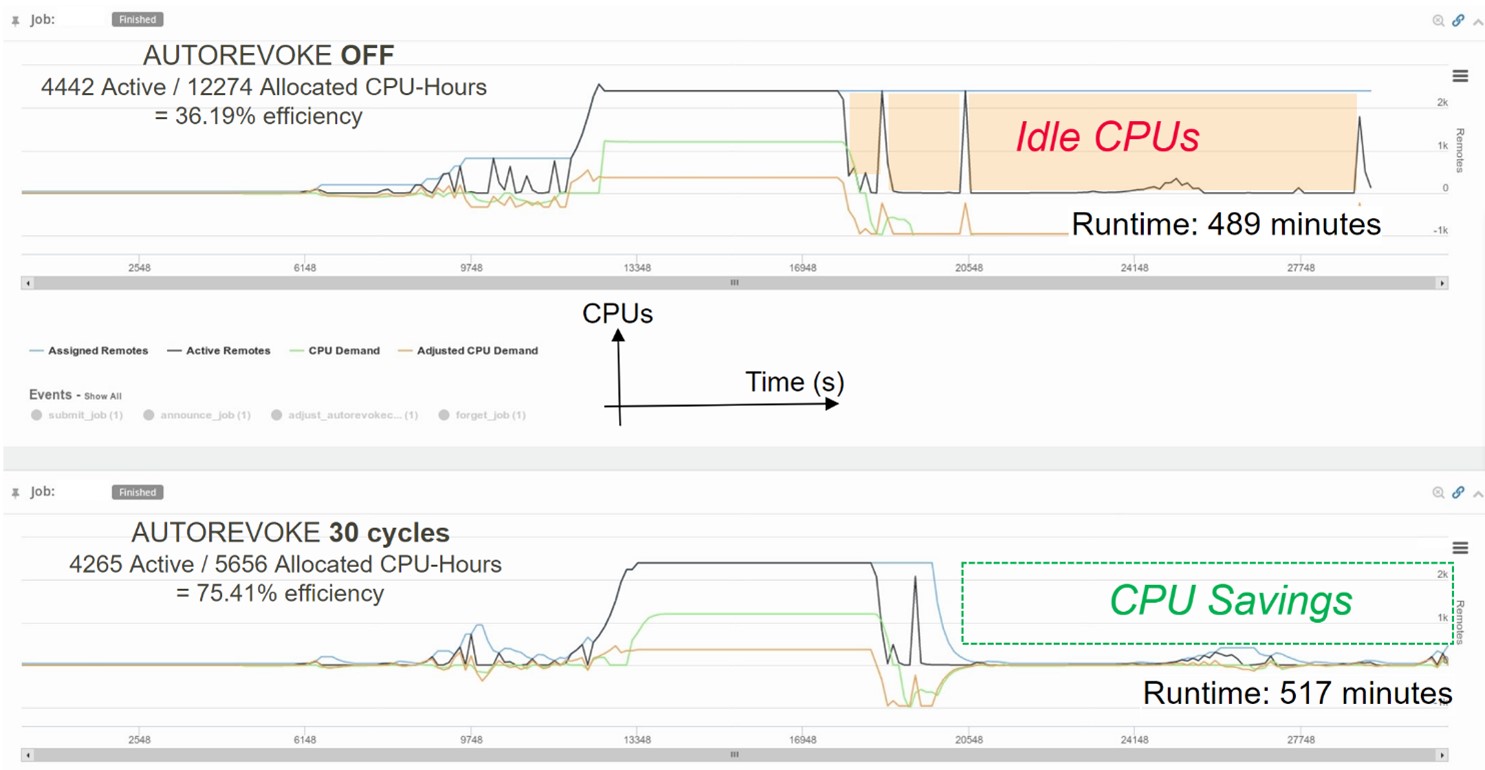
Cost savings through the power of spot instances
Adding to the cost-saving toolkit is the cloud’s ability to offer dynamic pricing. Foundries can now use spot instances to run high-performance tasks at a fraction of the regular cost. These spot instances, ideal for peak demand, tap into unused cloud capacity at lower rates, helping companies stay within budget without compromising performance.
FullScale processing: Speeding up time-to-tapeout
Cloud elasticity also shines with Calibre FullScale high-throughput processing capabilities, a compelling answer to the compute-intensive demands of PTOF. By enabling parallel lithography simulations, Calibre FullScale slashes job completion times, making faster tapeouts more attainable than ever. With the flexibility to adjust resources based on cost and performance needs, FullScale delivers optimal efficiency, ensuring every task is completed on schedule and with maximum precision (figure 2).
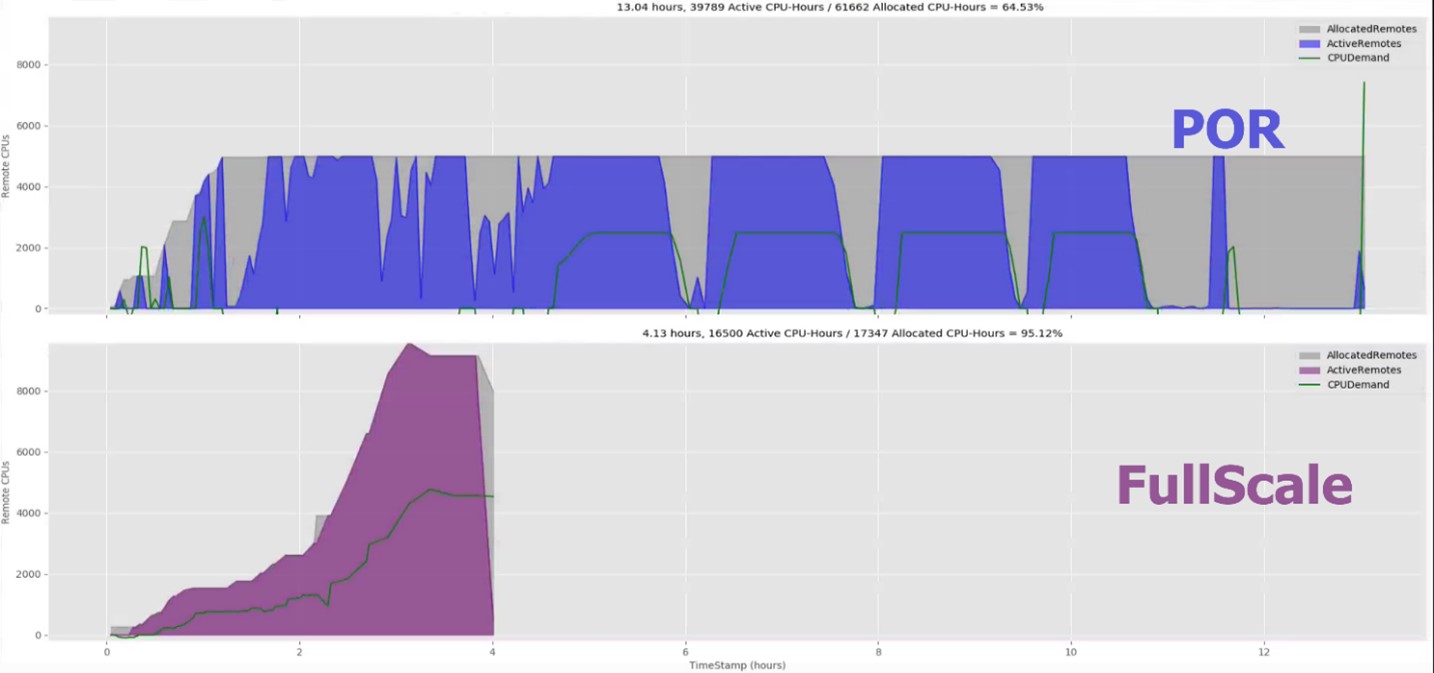
Tapping into GPU power: Acceleration for compute-intensive tasks
For leading-edge technology nodes, the availability of GPU instances in the cloud is a game-changer. Compute-intensive tasks—like lithography, etch, and e-beam simulations—now run with hardware-accelerated performance, reducing runtimes dramatically. With GPU acceleration, manufacturers can conduct highly detailed simulations that were previously limited by on-premises constraints. The cloud’s GPU capabilities bring precision and scale, redefining what’s possible in PTOF simulations.
Cloud-native orchestration: The Kubernetes advantage
Orchestration systems like Kubernetes are also part of this cloud-driven transformation. Siemens EDA’s solutions leverage container orchestration to enable seamless job distribution across cloud resources. With Kubernetes automating deployment, scaling, and workload management, running complex Calibre PTOF jobs becomes effortless, whether on-premises or in the cloud. This cloud-native execution model maximizes resource use, delivering scalability, efficiency, and flexibility for semiconductor manufacturers.
A new era for semiconductor manufacturing
As semiconductor manufacturing embraces the cloud, a new era is taking shape—one where agility, efficiency, and cost control redefine the way PTOF tasks are managed. With the flexibility to scale on demand, optimize budgets, and orchestrate workloads seamlessly, cloud-based PTOF workflows are setting new standards. By tapping into cloud capabilities, container orchestration, and GPU resources, semiconductor manufacturers gain the edge needed to drive innovation, speed time-to-market, and thrive in an ever-evolving industry.
For a deep dive into this PTOF cloud flow, please see the technical paper, Crush Semi-manufacturing runtimes with Calibre in the cloud.
Bassem is a cloud product engineer specializing in scalable and cost-efficient computing solutions for semiconductor design and manufacturing. With expertise in Kubernetes, high-performance computing, and cloud infrastructure, Bassem focuses on optimizing post-tapeout workflows, EDA tool deployment, and hybrid cloud strategies.
Also Read:
Getting Faster DRC Results with a New Approach
Full Spectrum Transient Noise: A must have sign-off analysis for silicon success
PSS and UVM Work Together for System-Level Verification
Averting Hacks of PCIe® Transport using CMA/SPDM and Advanced Cryptographic Techniques
Share this post via:
Comments
One Reply to “Unlocking the cloud: A new era for post-tapeout flow for semiconductor manufacturing”
You must register or log in to view/post comments.