fansink
Well-known member
The semiconductor industry is expanding rapidly as countries race to build new fabs. While it takes around 19 months to build a fab in Taiwan, it takes a whopping 38 months to build a fab in the U.S. due to the extensive time it takes to get a permit and because fabs are not constructed 24/7, according to Exyte, a leading engineering, construction, and design company that specializes in high-tech facilities like chip production plants, reports Semiconductor Digest.
Taiwan completes fabs in around 19 months, followed by Singapore and Malaysia at 23 months. European projects take 34 months, while the U.S. is the slowest at 38 months. A key reason for this is Taiwan's streamlined permit process and round-the-clock construction, whereas the U.S. and Europe face delays in approvals and do not construct 24/7. The U.S. has enacted a law that exempts certain U.S. fabs from federal environmental assessments, but that is obviously not enough to be on par with Taiwan.
Costs also differ widely. Constructing a plant in the U.S. is about twice as expensive as in Taiwan, despite similar equipment costs, according to Exyte. This discrepancy arises from higher labor costs, extensive regulatory requirements, and inefficiencies in supply chains. Also, Taiwanese workforce is highly experienced, so Taiwanese builders require fewer detailed blueprints because they are familiar with every step of the process, which speeds up completion of fab projects, according to Herbert Blaschitz, an executive at Exyte.
To compete efficiently with Taiwan — which has well-integrated supply chain, experienced workforce, and efficient regulatory processes — the U.S. and Europe must streamline permitting, optimize construction techniques, and adopt advanced planning tools like digital twins. Blaschitz suggests adopting 'virtual commissioning,' where a digital model of the plant is created before physical construction begins. This allows potential problems to be identified early, reducing costs and environmental impact while improving speed and efficiency.
Modern semiconductor production facilities are huge, both in terms of dimensions and investments. A leading-edge fab — such as those operated by Intel, Samsung Foundry, or TSMC — requires investment exceeding $20 billion, with $4-6 billion allocated just for the structure itself, according to Blaschitz, who highlighted Taiwan's advantages at the SEMI Industry Strategy Symposium.
The construction process involves 30-40 million workhours, using 83,000 tons of steel, 5,600 miles of electrical wiring, and 785,000 cubic yards of concrete, according to Blaschitz. A typical fab may include a 40,000-square-meter cleanroom with 2,000 production tools used for lithography, deposition, etching, cleaning, and other operations. Each of the tools requires around 50 individual utility and process connections.
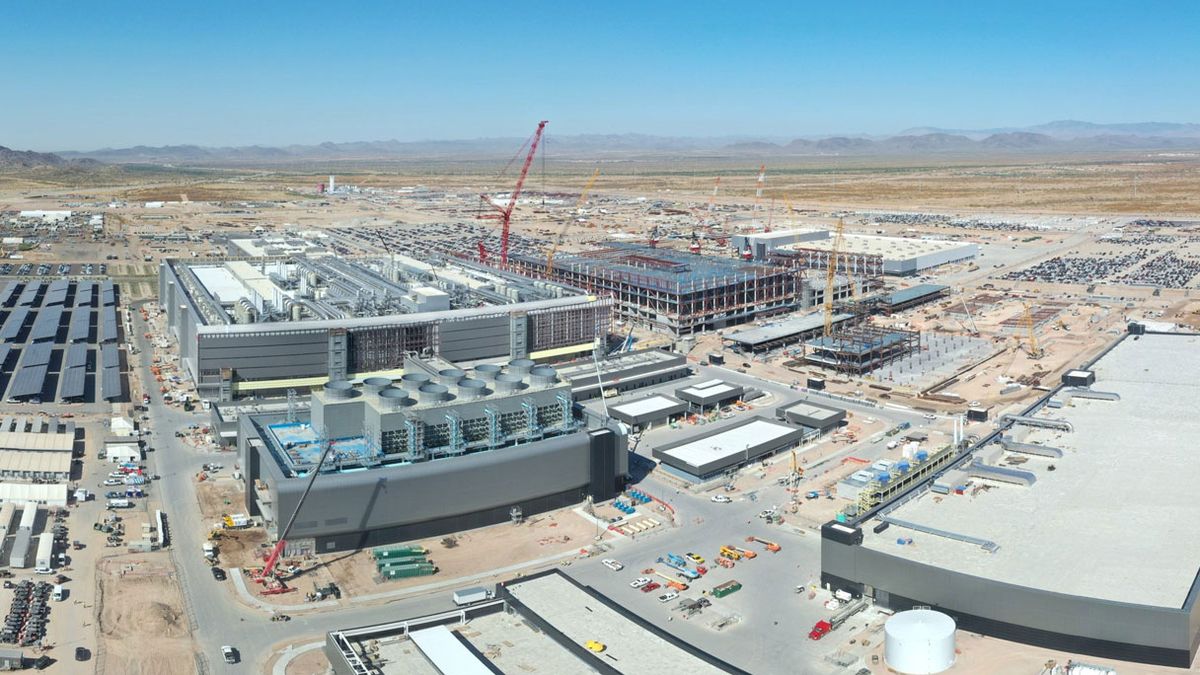
US fab construction costs twice as much, takes twice as long as Taiwan
U.S. and Europe need to adopt new construction techniques to be competitive.