Production Supervisor
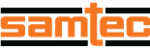
Website Samtec
Essential Functions/ Responsibilities:
- Responsible to manage, lead and supervise a team to achieve the organization objectives.
- Be the area owner and accountable for the area/section performance metric such as safety, quality, delivery, cost, ROCK (Remove, Organize, Clean, Keep), etc.
- Ensure the production team is clearly communicated with company policies, EHS (Environment, Health and Safety) and quality regulatory requirements and comply with it at all time.
- Responsible for End of Month (EOM) meeting in order to show and explain the work center results with the assemblers and let them know the corporate goals.
- Conduct regular 1:1 meeting, weekly stand up meeting with the associate as part of communication to provide/receive update, feedback and discuss about personal development and calibrate on expectation.
- Ensure a safe working environment for associates with enforcement on PPE (Personal Protection Equipment) compliance and LOTO (Lock Out Tag Out) application.
- Ensure product is produced according to the print in order to meet the industry standards and customer expectations for quality.
- Proactively look into quality improvement to ensure OD and PPM meet the corporate target.
- Contain and investigate any quality issue timely (together with MQS/technician etc.) in order to minimize the cost impact and escapee to customer.
- Responsible to support, work with and ensure OSS schedule the order according to the due date and batching opportunity, confirm material availability to deliver the order to customer timely.
- Work with OSS to manage the expedite system, rescheduling code and realistic date.
- Manage the machine capacity and people capacity (this includes the associate work schedule like OT, time off, vacation etc.) with alignment to the order schedule.
- Ensure orders are executed according to Samtec Golden Rule.
- Responsible for overall cost performance in your cost center. Manage the Over Time according to business requirement, drive for scrap and productivity improvement to reduce cost.
- Communicate to Techs on priority and engage them in troubleshooting defective tooling that may cause efficiency or quality concern.
- Walk the line frequently to know what is happening in the line and able to address the issue timely with the team.
- Monitor and review metric regularly and responsible to initiate, implement and work closely with relevant party to drive continuous improvement.
Required Experience:
- 3 – 5 Years’ Experience in Manufacturing, Production, or Supervision. Small part manufacturing is preferred.
- Strong in data analysis and is data driven.
- Experience with Process knowledge for related area.
- Excellent problem solving, investigation skills, and needs to be detail oriented.
- People management and leadership skills.
- Understand manufacturing concept, experience in Lean Manufacturing and Six Sigma is preferred.
- Must possess good communication skills – written & verbal.
- Must be able to use Microsoft Office Software (Word, Excel, Outlook, Access)
- Team player and must be able to work with multiple groups of people (Operators, Floor Managers, Engineers, etc.)
Preferred Education:
- Bachelor’s Degree in Engineering or other Technical discipline is required.
- Experience may be substituted for educational requirements.
Flynn Was Right: How a 2003 Warning Foretold Today’s Architectural Pivot