Facilities Maintenance Planner/Schedulers (MPS)
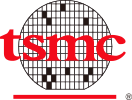
Website TSMC
We are seeking experienced Facilities Maintenance Planner/Schedulers (MPS) to join our growing team!
The Facilities Maintenance Planner/Scheduler (MPS) is responsible for ensuring that all maintenance activities are properly planned, scheduled in a timely and cost-effective manner. In addition, this position is responsible for ordering and managing all parts required for maintenance activities. To be successful in this role, a Facilities MPS should have strong organizational and time management skills, as well as excellent communication and problem-solving abilities. They should also have a background in maintenance and/or engineering and be familiar with maintenance management software and tools.
Responsibilities:
The Facilities MPS is responsible for planning and scheduling maintenance activities for the facility and organization. They work closely with technicians, engineers, and management to ensure that maintenance tasks are completed in a timely and efficient manner.
The Facilities MPS will develop and maintain a maintenance schedule for equipment and facilities utilizing the Computerized Maintenance Management System (CMMS).
Responsibilities will include:
- Develop and maintain a comprehensive maintenance plan and schedule for all equipment and facilities to reduce downtime and increase efficiency.
- Order and manage all parts required for maintenance activities, ensuring that parts are available when needed and that inventory levels are maintained.
- Apply system understanding and knowledge alongside CMMS to plan and schedule all maintenance activities, including preventive maintenance, corrective maintenance, and predictive maintenance.
- Training technicians, engineers, and management employees on usage of CMMS.
- Creating work orders and assigning tasks to technicians and contractors to ensure that all maintenance work is executed in accordance with the maintenance plan and schedule.
- Monitoring and tracking the progress of maintenance tasks to ensure they are completed on time.
- Identifying and ordering necessary parts, tools, and equipment for maintenance activities.
- Communicating with internal and external stakeholders to plan and schedule maintenance activities to minimize downtime and disruptions to production schedules.
- Analyzing data, metrics, and trends to identify opportunities for improvement in maintenance processes/procedures and make recommendations to management.
- Develop and maintain accurate documentation related to maintenance activities, including work orders, maintenance logs, and equipment histories.
- Ensure all requirements as specified by the manufacturer of equipment systems are met, and equipment operations, repairs, modifications, and maintenance meet environmental protection and safety requirements.
- Additional duties based on business needs, including Emergency Response Team (ERT).
Knowledge and Personal skills:
The Facilities MPS must have knowledge of industry standards, codes and regulations, and the ability to apply to maintenance operations of site systems.
- Always follow all safety policies and procedures.
- Ability to read, interpret, and understand engineering drawings and specifications.
- Ability to work cooperatively with other technicians, engineers, and management.
- Excellent communication and interpersonal skills.
- Analytical and problem-solving skills.
- Sound decision making skills.
- Effective written, verbal, presentation, and listening communications skills.
- Computer skills including the ability to operate corporate email, spreadsheets, word processing, and engineering drawing databases at a highly proficient level.
- Experience in maintenance planning/scheduling and parts ordering.
- Capable of working independently and exhibit effective time management skills.
- Willingness and ability to work overtime when needed for business purposes, or to be called-in to work in the event of emergency or business needs.
- Contributes recommendations and suggestion for work method improvements, safety, materials, and tools.
- Attributes should include honesty, trustworthiness, respect for others, flexibility, and sound workplace ethics.
- Duties will include any and all other directions of supervision that can safely be performed by the incumbent.
Experience, Education, and Training:
- High School graduation or GED is required.
- 2-5+ years previous experience managing Computerized Maintenance Management Systems (CMMS) is required.
- Experience utilizing IBM Maximo is a plus.
- 8-10+ years previous experience of one or more of the following facilities operations and maintenance disciplines is required (descriptions below are not all inclusive):
- Mechanical systems: Chillers, boilers, Airborne Molecular Contaminants (AMC), local air abatement, air scrubbers
- Electrical systems: switchgears, breakers, NFPA 70E, arc flash
- Instrumentation and Controls systems: PLC, SCADA, ladder logic, network communications, DCS
- Gas, Chemical, and Slurry systems: Hazardous Production Materials (HPM), bulk gas and chemical distribution, gas/chemical analyzers
- Water Treatment systems: Ultrapure Water (UPW), industrial wastewater treatment, acid neutralization, precipitation systems, dewatering systems, environmental/regulatory requirements
- Technical College or Trade Program is preferred. An engineering bachelor’s degree is not required but is a plus.
Physical Requirements:
- Spending extended hours working inside and outside in all weather conditions, and in awkward body positions which can cause physical discomfort and strain.
- Regularly lift up to 50 lbs and to adjust heavy objects.
- Contact with sharp, hot, and cold equipment and parts.
- Must be medically qualified to wear a personal respirator.
- Sensory demands include exposure to the smells associated with industrial chemical operations, exposure to the sounds associated with powered tools and industrial equipment.
- Must have the ability to safely climb ladders, and work at elevation from ladders, scaffolding, lifts, roofs, or platforms, and the ability to work in confined spaces.
Flynn Was Right: How a 2003 Warning Foretold Today’s Architectural Pivot