TSMC is the world’s largest chipmaker. They make chips for a wide range of industries, from smartphones to cars to data centers. Their chips are in almost every piece of technology we use in our daily lives. This makes TSMC very busy, and they are constantly producing chips. However, even this is not enough, as the production capacity of their new Kumamoto factory is already fully booked before it has even started mass production. Here are the details…
TSMC and Sony Partner to Meet Growing Demand for Automotive Chips
TSMC is always looking for ways to meet the ever-increasing demand for its chips. To do this, the company not only upgrades its existing production facilities, but also builds new ones. One of these new facilities is the Kumamoto factory in Japan. The Kumamoto factory cost TSMC more than $8.6 billion to build. It is scheduled to start mass production in 2024 and will employ around 1,700 people. The project is so big and important that it was a collaboration between TSMC and Sony Semiconductor Solutions.
Sony and TSMC has indicated that the demand for semiconductors will outstrip the supply that can be provided by the TSMC Kumamoto plant. This news has been revealed by Terushi Shimizu, President and CEO of Sony Semiconductor Solutions. The plant has already received a large order from Honda, and the increasing interest in electric vehicles is expected to lead to even more orders. Industry experts believe that the partnership between Sony and TSMC will help the plant reach its full capacity early on.
Moreover, this isn’t the only possible solution. One possibility is that TSMC will build a second wafer production facility in Japan. TSMC’s chairman, Mark Liu, has said that the company is considering this option, but no final decision has been made. If TSMC does decide to build a second plant in Japan, it would likely be located near the current plant in Kumamoto. The Japanese government is eager to attract more investment from TSMC, so it is expected to offer the company substantial subsidies.
TSMC and Sony Partner to Meet Growing Demand for Automotive Chips
TSMC is always looking for ways to meet the ever-increasing demand for its chips. To do this, the company not only upgrades its existing production facilities, but also builds new ones. One of these new facilities is the Kumamoto factory in Japan. The Kumamoto factory cost TSMC more than $8.6 billion to build. It is scheduled to start mass production in 2024 and will employ around 1,700 people. The project is so big and important that it was a collaboration between TSMC and Sony Semiconductor Solutions.
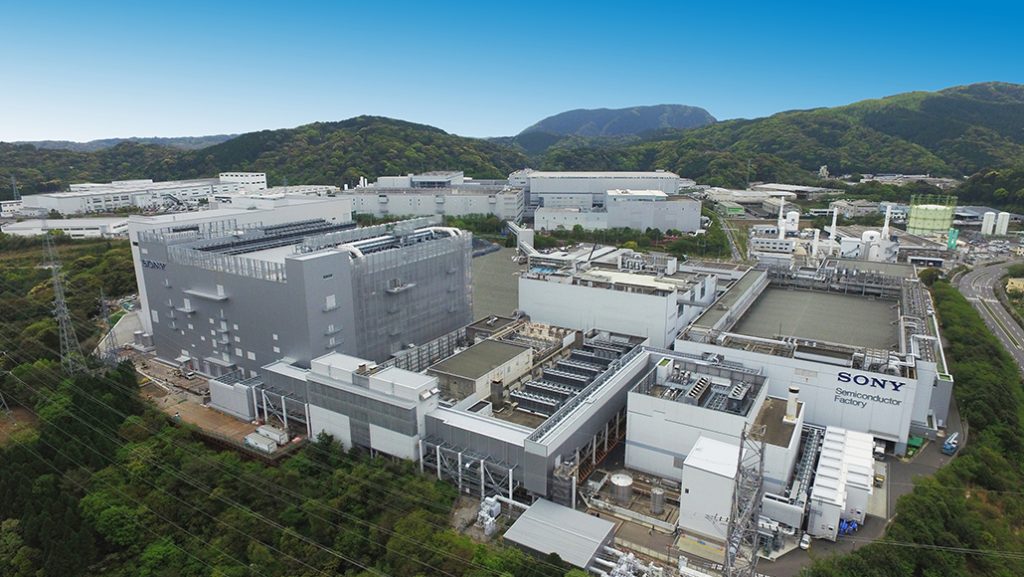
Sony and TSMC has indicated that the demand for semiconductors will outstrip the supply that can be provided by the TSMC Kumamoto plant. This news has been revealed by Terushi Shimizu, President and CEO of Sony Semiconductor Solutions. The plant has already received a large order from Honda, and the increasing interest in electric vehicles is expected to lead to even more orders. Industry experts believe that the partnership between Sony and TSMC will help the plant reach its full capacity early on.
Moreover, this isn’t the only possible solution. One possibility is that TSMC will build a second wafer production facility in Japan. TSMC’s chairman, Mark Liu, has said that the company is considering this option, but no final decision has been made. If TSMC does decide to build a second plant in Japan, it would likely be located near the current plant in Kumamoto. The Japanese government is eager to attract more investment from TSMC, so it is expected to offer the company substantial subsidies.