hist78
Well-known member
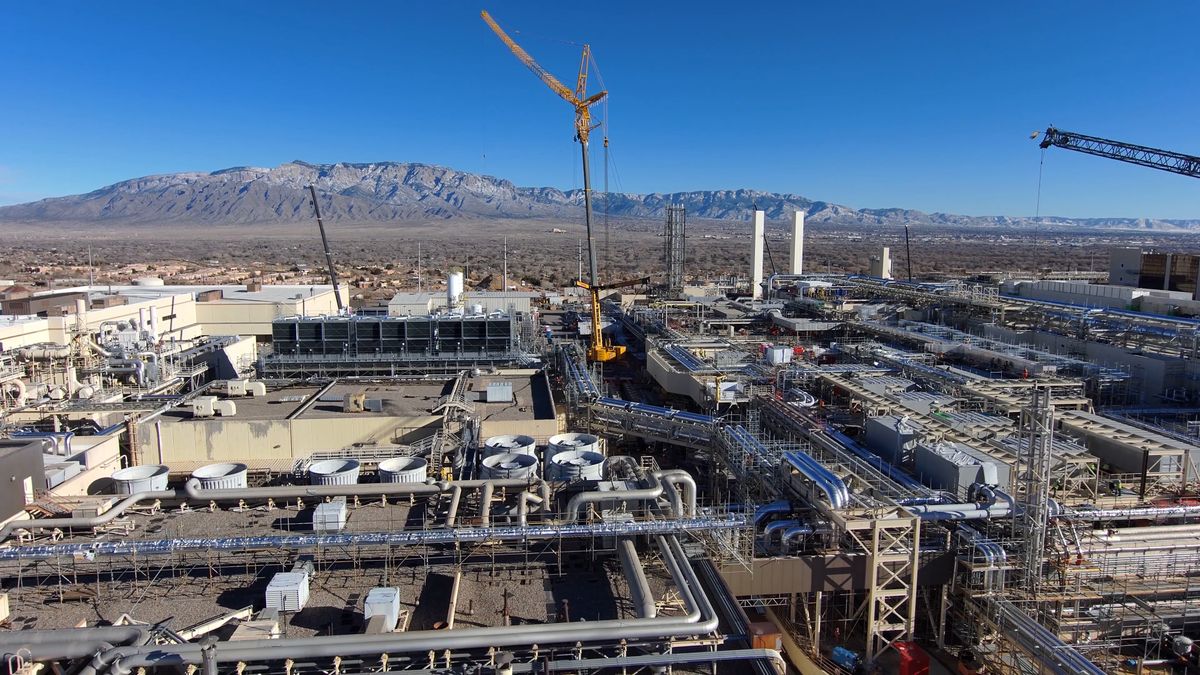
U.S. chip fab construction is among the slowest in the world -- a complex web of regulations is to blame according to study
It's kind of a mess.
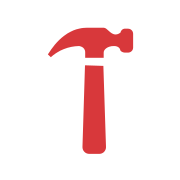
Array ( [content] => [params] => Array ( [0] => /forum/threads/u-s-chip-fab-construction-is-among-the-slowest-in-the-world-a-complex-web-of-regulations-is-to-blame-according-to-study.19635/ ) [addOns] => Array ( [DL6/MLTP] => 13 [Hampel/TimeZoneDebug] => 1000070 [SV/ChangePostDate] => 2010200 [SemiWiki/Newsletter] => 1000010 [SemiWiki/WPMenu] => 1000010 [SemiWiki/XPressExtend] => 1000010 [ThemeHouse/XLink] => 1000970 [ThemeHouse/XPress] => 1010570 [XF] => 2021770 [XFI] => 1050270 ) [wordpress] => /var/www/html )
Mils for PCB rules. Just don't get me started... :-(I didn't really propose a solution, did I? It's not changing the regulations or eliminating regulations. If you were to change something it would make the problem worse; it would create uncertainty. Possibly cause a crash. US regulations aren't really the issue in my opinion. A fab is a "global product"--while located in one place, it has to work in a country of origin (the US, Korea, or Taiwan) and one or two other countries, duplicating the original. Things as basic as the fab shape and number of stories change in translating from one country to another.
So what is needed is greater knowledge of localization strategies in engineering education. You see this a bit with power supplies--they work with multiple plugs and cycles and voltage ranges. Localization engineering is mostly ad hoc, doesn't exist as a discipline currently. As a branch of the major disciplines, we need more engineers who are fluent in the global standards, the unique gaps between foreign and domestic, and how to bridge. No silver bullet solutions here, sadly.
It would help if the US would work on harmonization with global standards. We have our own unique units, our own unique building codes, and that's fine, as I said above, don't change anything. But there is room for some gradual, well planned out transitions and opening up to the global standards. I expect the more highly engineered products like EVs built in Mexico will usher in the global standards through the southern door. So this will happen whether we like it or not, and politicians are acting like it's the end the world already. Metric units are coming! Oh no!
Imperial units are just one of the things we need to modernize and harmonize. But its a slow, slow process. We should recognize our global competitiveness depends on pulling our heads out of the sand.