By Jeff Butts published 16 hours ago
Worker treatment that's acceptable in Taiwan simply won't be tolerated by US employees
Taiwan Semiconductor Manufacturing Company (TSMC), one of the world’s largest advanced computer chip manufacturers, continues finding its efforts to get its Arizona facility up and running to be more difficult than it anticipated. The chip maker’s 5nm wafer fab was supposed to go online in 2024 but has faced numerous setbacks and now isn’t expected to begin production until 2025. The trouble the semiconductor has been facing boils down to a key difference between Taiwan and the U.S.: workplace culture. A New York Times report highlights the continuing struggle.
One big problem is that TSMC has been trying to do things the Taiwanese way, even in the U.S. In Taiwan, TSMC is known for extremely rigorous working conditions, including 12-hour work days that extend into the weekends and calling employees into work in the middle of the night for emergencies. TSMC managers in Taiwan are also known to use harsh treatment and threaten workers with being fired for relatively minor failures.
TSMC quickly learned that such practices won’t work in the U.S. Recent reports indicated that the company’s labor force in Arizona is leaving the new plant over these perceived abuses, and TSMC is struggling to fill those vacancies. TSMC is already heavily dependent on employees brought over from Taiwan, with almost half of its current 2,200 employees in Phoenix coming over as Taiwanese transplants.
The move to begin manufacturing chips in Arizona was seen as one way to boost advanced chip-making in the U.S. and reduce reliance on Taiwan imports. Given rising tensions between the United States, China, and Taiwan, this is considered to be of vital importance. U.S. Commerce Secretary Gina M. Raimondo says the country purchases 92 percent of its most advanced chips from Taiwan.
TSMC has committed $65 billion to the project, The New York Times notes. Furthermore, the facility has a $6.6 billion grant from the U.S. government under the CHIPS and Science Act.
The plan is to create 6,000 jobs as TSMC builds out the rest of the facility. Ultimately, TSMC will have three different factories at its Phoenix campus, and it desperately wants to reduce the ratio of Taiwanese immigrants to local hires.
“We want to make this site a successful site and a sustainable site,” according to Richard Liu, director of employee communications and relations at the Arizona site. “Sustainable means that we cannot keep relying on Taiwan sending people here.”
www.tomshardware.com
Worker treatment that's acceptable in Taiwan simply won't be tolerated by US employees
Taiwan Semiconductor Manufacturing Company (TSMC), one of the world’s largest advanced computer chip manufacturers, continues finding its efforts to get its Arizona facility up and running to be more difficult than it anticipated. The chip maker’s 5nm wafer fab was supposed to go online in 2024 but has faced numerous setbacks and now isn’t expected to begin production until 2025. The trouble the semiconductor has been facing boils down to a key difference between Taiwan and the U.S.: workplace culture. A New York Times report highlights the continuing struggle.
One big problem is that TSMC has been trying to do things the Taiwanese way, even in the U.S. In Taiwan, TSMC is known for extremely rigorous working conditions, including 12-hour work days that extend into the weekends and calling employees into work in the middle of the night for emergencies. TSMC managers in Taiwan are also known to use harsh treatment and threaten workers with being fired for relatively minor failures.
TSMC quickly learned that such practices won’t work in the U.S. Recent reports indicated that the company’s labor force in Arizona is leaving the new plant over these perceived abuses, and TSMC is struggling to fill those vacancies. TSMC is already heavily dependent on employees brought over from Taiwan, with almost half of its current 2,200 employees in Phoenix coming over as Taiwanese transplants.
The move to begin manufacturing chips in Arizona was seen as one way to boost advanced chip-making in the U.S. and reduce reliance on Taiwan imports. Given rising tensions between the United States, China, and Taiwan, this is considered to be of vital importance. U.S. Commerce Secretary Gina M. Raimondo says the country purchases 92 percent of its most advanced chips from Taiwan.
TSMC has committed $65 billion to the project, The New York Times notes. Furthermore, the facility has a $6.6 billion grant from the U.S. government under the CHIPS and Science Act.
The plan is to create 6,000 jobs as TSMC builds out the rest of the facility. Ultimately, TSMC will have three different factories at its Phoenix campus, and it desperately wants to reduce the ratio of Taiwanese immigrants to local hires.
“We want to make this site a successful site and a sustainable site,” according to Richard Liu, director of employee communications and relations at the Arizona site. “Sustainable means that we cannot keep relying on Taiwan sending people here.”
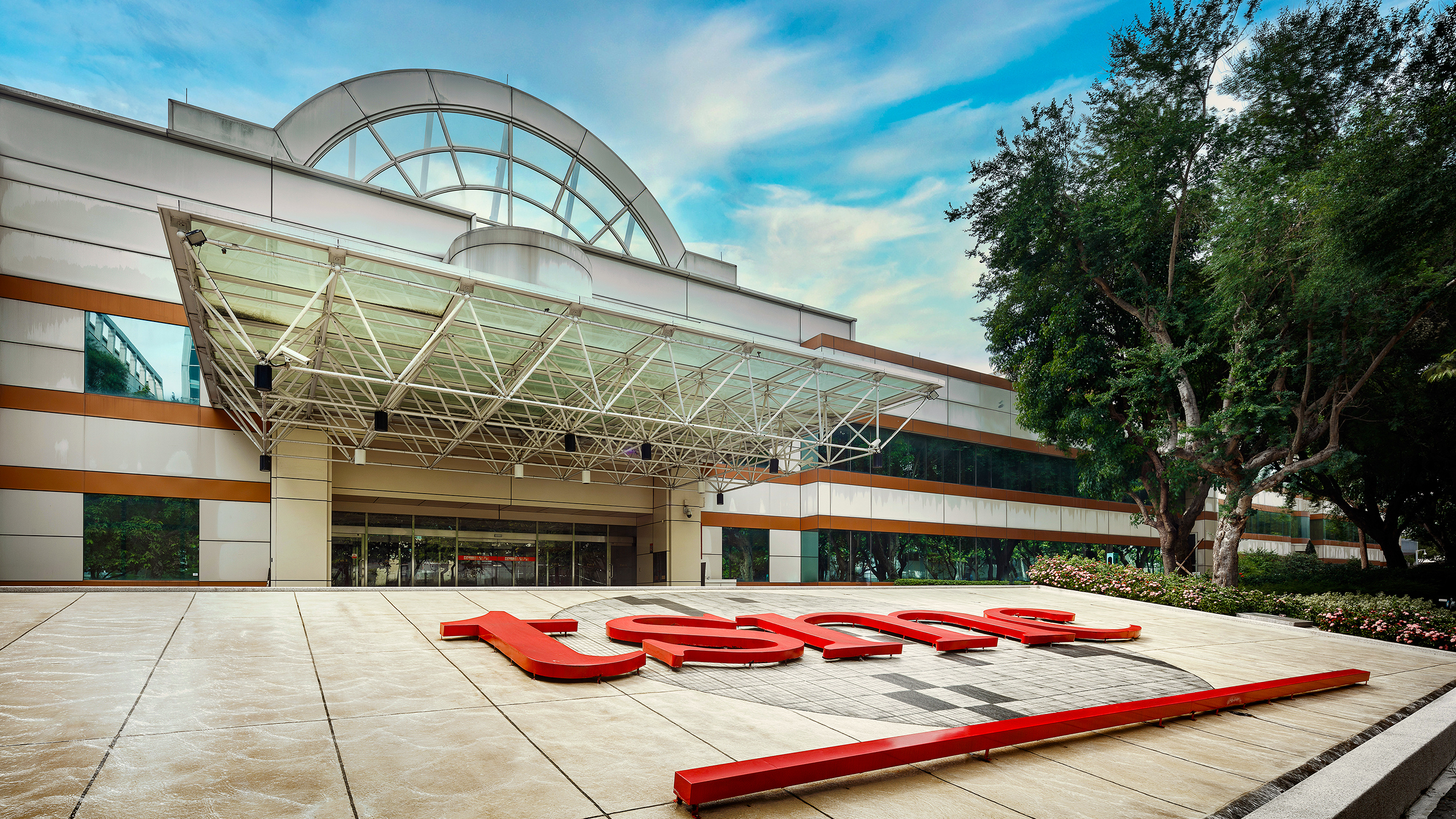
TSMC Arizona struggles to overcome vast differences between Taiwanese and US work culture
Worker treatment that's acceptable in Taiwan simply won't be tolerated by US employees