Demand for wafer fab equipment has been proliferating in recent years, which is why fab toolmakers' revenues have also been setting records. As it turns out, last year, ASML became the world's largest maker of fab tools, dethroning Applied Materials, which was a leader for decades, as observed by analyst Dan Nystedt. While this is hardly competition and there are several reasons why ASML came first, it is a remarkable turn of events.
ASML earned $29.83 billion in calendar 2023, whereas Applied's revenue achieved $26.52 billion, according to Nystedt. There are several things to keep in mind here. Firstly, ASML's financial year follows the calendar year, whereas Applied Materials's 2023 financial year ended October 29, 2023. This is why the analyst used the company's Q1 FY2024 results (which ended on January 28, 2024) for his calculations.
(Image credit: Dan Nystedt/Twitter)
While this is not exactly an apples-to-apples comparison, since ASML won by billions, this is a reasonable comparison that reflects the trends.
There are multiple reasons why ASML managed to take away the fab toolmaking crown from Applied Materials. First up, the company recognized revenue for 53 Low-NA EUV Twinscan NXE tools (up from 40 in 2022), each of which costs roughly $183 million. In addition, the company recognized revenue for 125 deep ultraviolet lithography tools (up from 81 a year before). Secondly, ASML could sell sophisticated tools to Chinese customers for most of calendar 2023 as sanctions against the Chinese semiconductor sector kicked in only in September and only for one tool. By contrast, sales of tools to Chinese clients by Applied Materials were, to a degree, impacted by the U.S. export rules introduced in October 2023.
While the turn of the tables is outstanding, this is really not a competition because Applied Materials does not produce lithography equipment. In contrast, ASML does not make tools for epitaxy, ion implant, deposition, and selective materials removal. Meanwhile, virtually no fabs today can run without equipment from Applied Materials, ASML, KLA, and Tokyo Electron, so these companies would rather complement each other. Furthermore, the more ASML tools sold, the more Applied's equipment is required, so both companies are set to thrive in the coming years.
www.tomshardware.com
ASML earned $29.83 billion in calendar 2023, whereas Applied's revenue achieved $26.52 billion, according to Nystedt. There are several things to keep in mind here. Firstly, ASML's financial year follows the calendar year, whereas Applied Materials's 2023 financial year ended October 29, 2023. This is why the analyst used the company's Q1 FY2024 results (which ended on January 28, 2024) for his calculations.
(Image credit: Dan Nystedt/Twitter)
While this is not exactly an apples-to-apples comparison, since ASML won by billions, this is a reasonable comparison that reflects the trends.
There are multiple reasons why ASML managed to take away the fab toolmaking crown from Applied Materials. First up, the company recognized revenue for 53 Low-NA EUV Twinscan NXE tools (up from 40 in 2022), each of which costs roughly $183 million. In addition, the company recognized revenue for 125 deep ultraviolet lithography tools (up from 81 a year before). Secondly, ASML could sell sophisticated tools to Chinese customers for most of calendar 2023 as sanctions against the Chinese semiconductor sector kicked in only in September and only for one tool. By contrast, sales of tools to Chinese clients by Applied Materials were, to a degree, impacted by the U.S. export rules introduced in October 2023.
While the turn of the tables is outstanding, this is really not a competition because Applied Materials does not produce lithography equipment. In contrast, ASML does not make tools for epitaxy, ion implant, deposition, and selective materials removal. Meanwhile, virtually no fabs today can run without equipment from Applied Materials, ASML, KLA, and Tokyo Electron, so these companies would rather complement each other. Furthermore, the more ASML tools sold, the more Applied's equipment is required, so both companies are set to thrive in the coming years.
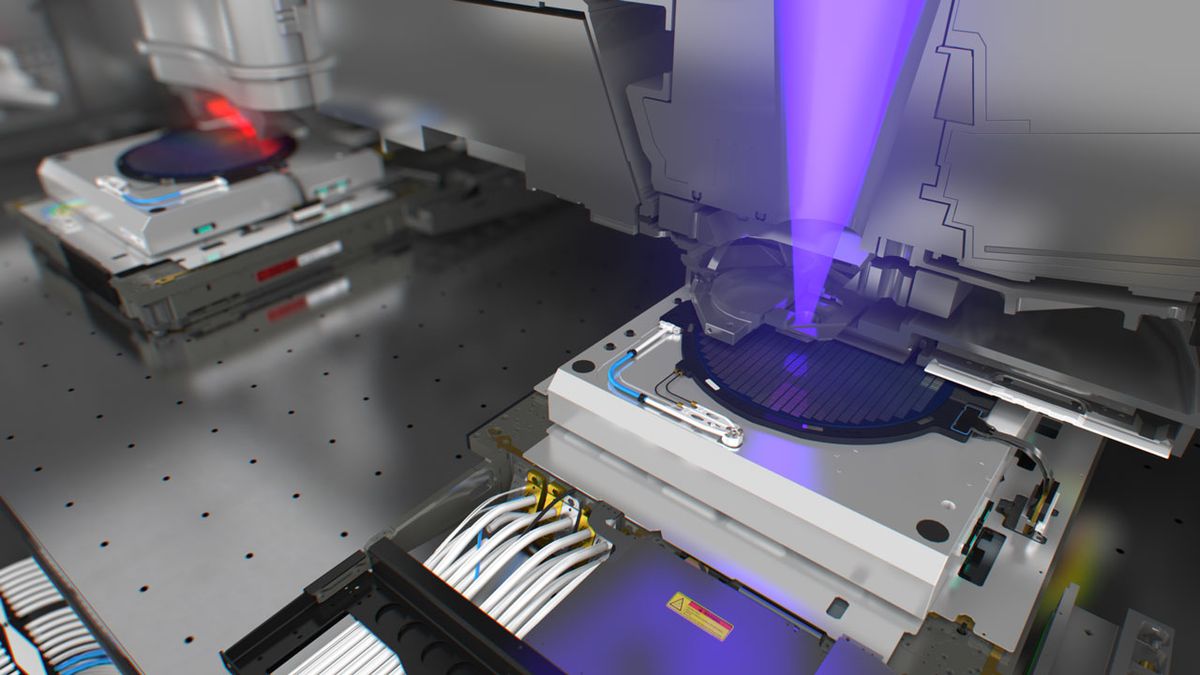
ASML dethrones Applied Materials, becomes world's largest fab tool maker: analyst
ASML gets 2023 chipmaking equipment crown.
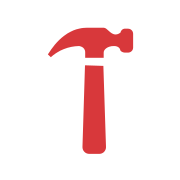